Research team seeks to eliminate cost, technical barriers to adoption of biobased plastic packaging
By introducing additives to improve plastic flow and developing techniques to reduce wall thickness, Netherlands-based SFA Packaging (Middelharnis), in collaboration with university researchers, hopes to make biobased plastic a viable option for food packaging.
July 6, 2017
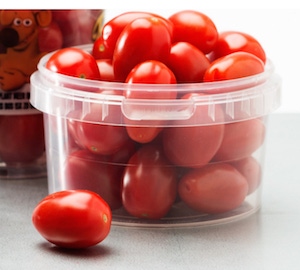
A new research project aims to produce price-competitive transparent food packaging made of biobased plastics—materials that are normally less-than-ideal candidates for injection molding of thin-walled packages.
Food producers’ interest in biobased plastic packaging tends to evaporate when they calculate the cost of switching to these materials. At the same time, however, “everyone feels that there should be more environmentally friendly packaging available,” says Niels L’Abée, director of Netherlands-based SFA Packaging (Middelharnis), a supplier of injection molded packaging for the food industry.
So L’Abée and Wageningen Food & Biobased Research, a contract research arm of Wageningen University & Research in the Netherlands, decided to study whether commercially available biobased plastics could be made more attractive as food-packaging options.
Though they are strong and stiff enough for food-packaging film, biobased plastics are usually too viscous for thin-wall injection molding. The project partners will try to change that with additives that improve plastic flow.
In addition, the partners will investigate sophisticated procedures capable of producing biobased packaging with even thinner walls than those made of conventional plastics. This is crucial because reducing packaging wall thickness is the only way to cut packaging material consumption and cost.
Since biobased plastic displays only limited effectiveness as a water-vapor barrier, the partners will also try adding an extra packaging layer that provides the barrier properties required to keep food fresh.
Another key aim of the project is to develop biobased plastic packaging that can be profitably manufactured with around half the CO2 emissions that result from the production of conventional plastics.
The partners hope to have a product on the market within two years. How much more will consumers be willing to spend for a greener alternative to conventional food packaging? “We have no idea,” L’Abée admits, adding that the partners are undertaking the development of biobased packaging at their own risk “and hope we will succeed and, in the end, can sell it.”
About the Author(s)
You May Also Like