Low-carbon, Eco-friendly Materials on Show at Chinaplas
The automotive sector is the main target market for bio-based and other sustainable materials.
March 16, 2024
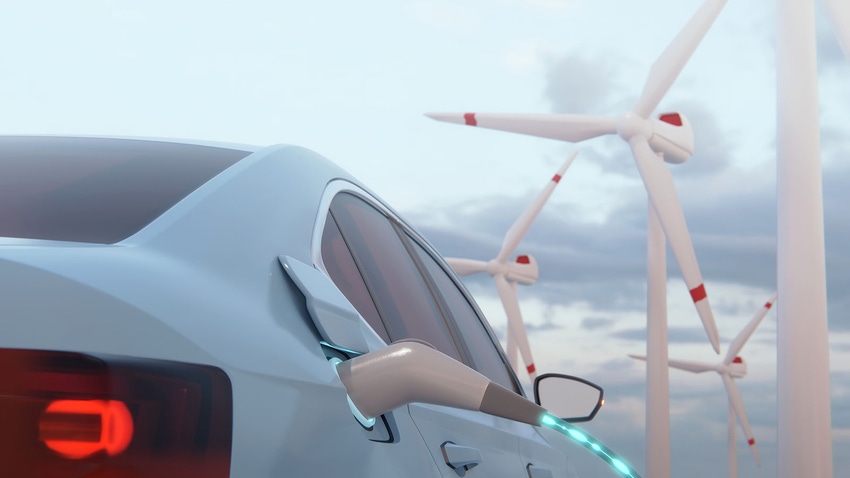
At a Glance
- Recycled plastics usage grows in automotive
- Bio-based materials also coming into play
- Several OEMs commit to hydrogen
Carbon-emission reduction has become a buzzword in the automotive industry. BMW, Volvo, Volkswagen, Benz, Great Wall, Geely, and other automakers have announced their targets and action plans for carbon neutrality. Using low-carbon and eco-friendly materials, such as recycled plastics, bio-based compounds, and spray-free materials, is one of the most important measures for automakers to reduce carbon emissions.
Regarding recycled plastics:
BMW and Volkswagen are gradually increasing the proportion of recycled plastics in new cars;
Honda and Toray are exploring the potential application of chemically recycled polyamide (PA) 6 in the automotive sector;
Magna has introduced a mono-material, 100% recyclable plastic for car seat foam cushion and trim parts.
Bio-based cooling
Bio-based materials are also coming into play in the auto sector in recent years. For example, concept cars such as Kia's EV3 and EV4 use natural fibers and mycelium to reduce their carbon footprint. Polestar and Röchling are ready to launch the first bio-based thermal management cooling system.
Paint-free materials
Using paint-free materials is also an effective way to reduce carbon emissions. One of Toyota's interiors, for example, uses BASF's paint-free PA, while Honda has joined hands with Mitsubishi Chemical to develop paint-free colored PMMA that can be used for car bodies and interiors.
Many other examples demonstrate that automakers, parts manufacturers, and materials suppliers are collaborating across the value chain to develop a sustainable roadmap for automotive plastics.
Hydrogen fuel cell cars on track
Despite reservations from some quarters, a number of automakers maintain that hydrogen energy is an inevitable choice for the strategic transformation of carbon neutrality. Hydrogen vehicles can be refueled in just four to five minutes and have a driving range up to 500 km (310 miles).
The BMW iX5 hydrogen fuel cell car has completed road testing in Europe and Hyundai’s Nexo boasts the highest sales volume for that category in the world, while Toyota’s Crown sedan is equipped with three hydrogen storage tanks and has an impressive driving range reaching 820 km (510 miles).
Hydrogen storage tanks, which are indispensable for hydrogen vehicles, are mostly made of carbon-fiber composites:
Toray's high-strength carbon fiber is used for high-pressure hydrogen storage cylinders for 70 MPa vehicles;
Evonik's Vestamin curing agent is used for epoxy systems, and the company’s Ancamine curing agent can be used for rapid infiltration of carob fiber, thereby enabling a 70% weight reduction for the tank.
Hydrogen storage tank liners require polymers with strong hydrogen barrier properties to prevent leakage. Arkema's Rilsan PA11 is one such material that can be used to produce high-pressure hydrogen storage cylinder liners that are resistant to low temperatures and high-pressure hydrogen blistering.
This article is an edited and abridged version of source material provided by Adsale Plastics Network.
About the Author(s)
You May Also Like