Polypropylene Makes Its Case for EV Lightweighting, Circularity
ExxonMobil says a reduction in filler levels, superior paint-free aesthetics, and advanced recycling are the keys to enhanced electric vehicle range and recyclability.
December 12, 2023
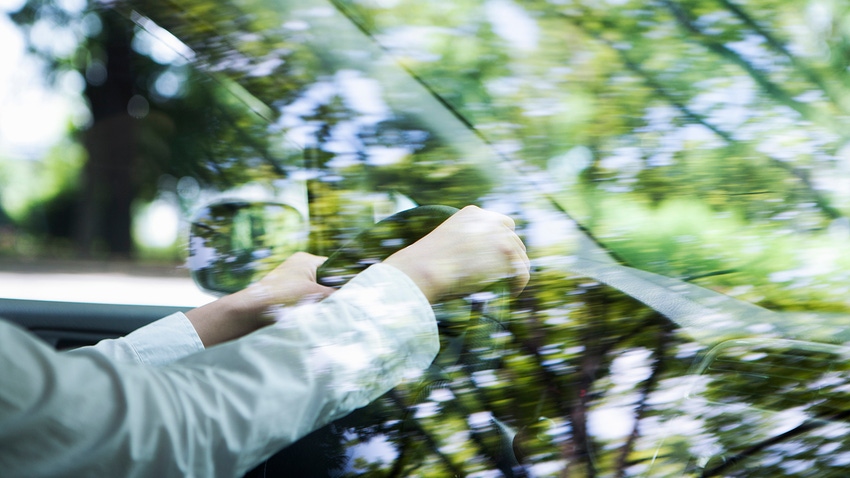
At a Glance
- Increased use of PP in EV-specific components
- Color-at-press consolidates materials usage
- Advanced recycling optimal for safety critical components
Electric vehicle (EV) OEMs need to convince consumers of the driving range credentials of their cars. While the obvious solution is to throw in bigger batteries with higher energy storage, increased use of plastics remains one key to solving the issue of range anxiety.
One way to achieve this is to optimize material design to fit the technical needs of particular interior and exterior parts, according to ExxonMobil.
Speaking to PlasticsToday in an exclusive interview, Olivier Lorge, global marketing manager for polypropylene, Vistamaxx, and Exact (PVE) at ExxonMobil, noted additional trends have emerged in the EV plastics space. He cited the increased use of polypropylene (PP) in EV-specific components such as frunks and battery cases, materials consolidation throughout the vehicle, and greater content of recycled material in automotive compounds.
Coloring at the press
“Color-at-press, or mold-in-color, injection molding using masterbatches has been around for some time in North America but that’s not the case in Europe and Asia,” notes Lorge. “[Using this process] you get thinner and lighter parts. We’ve developed an improved grade, Achieve Advanced PP8285E1, to use in this neat resin injection molding for rigid interior trim including seat trim, quarter trim panels, lower pillars, and door panels.”
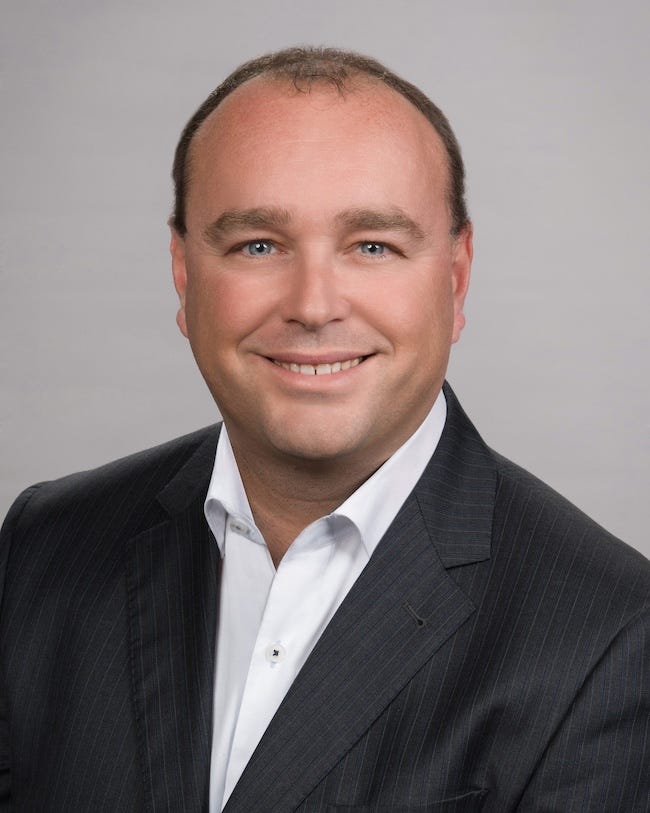
"It's not yet clear how advanced recycling will be counted in the European Directive, but I hope pragmatism will prevail," said Olivier Lorge of ExxonMobil.
Achieve Advanced PP8285E1 is a medium flow [MFR 30] PP impact copolymer grade exhibiting stiffness and withstanding impact at low temperature. Adds Lorge, “This is the next step to make the car lighter, especially in Asia and Europe where compounding is widely used.”
New ICP grades for better flow
Without the internal combustion engine (ICE) occupying space under the hood, EV OEMs are free to use this area for storage purposes, leading to the development of a large frunk (front trunk). Here too, the emphasis is on using polypropylene to lightweight the application as much as possible, but also ensure the material fills out the really large part designs. “An issue with thin-wall molding of large parts such as bumper fascia is that long flow length can lead to the phenomenon of tiger stripes, which in turn results in rejects or rework,” says Lorge. “To solve this issue, we’ve developed a new grade called Achieve Advanced PP7985E1, which is a high-flow [MFR 65], high-stiffness impact copolymer providing a superior aesthetic solution for black-colored parts.” A video of this solution can be viewed here.
EVs take the circular route
Consolidation of materials in vehicles has an additional positive implication — namely, similar materials are easier to recycle. The European Union (EU) is pushing for a 25% recycled content mandate in automobiles, and Lorge thinks that some parts such as interior trim may be able to accommodate more of such a mechanically recycled component, particularly when ExxonMobil’s Vistamaxx performance polymer is employed as a compatibilizer.
However, for safety-critical parts such as dashboards and bumpers, lower levels may be achievable when considering driver, passenger, and pedestrian wellbeing as well as part quality itself. “We believe that advanced [or chemical] recycling is an effective solution to complement mechanical recycling to achieve the recycled content requirement,” says Lorge. He concludes, “It's not yet clear how advanced recycling will be counted in the European Directive, but I hope pragmatism will prevail and that we can have the technology as part of the solution.”
About the Author(s)
You May Also Like