Resin Enables Cost-Effective Impact Modification with Lighter Elastomer Load
ExxonMobil Chemical and compounder Kingfa have co-developed a formulation with less elastomer that meets required automotive impact properties without performance or processing trade-offs.
May 27, 2022
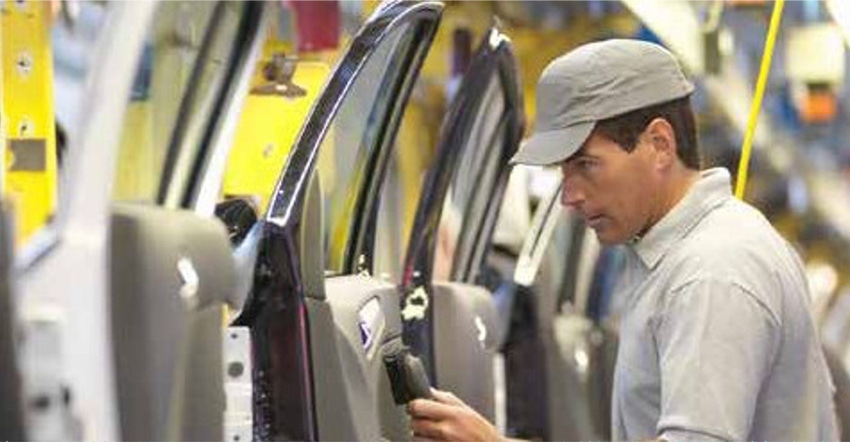
Polyolefin elastomers (POEs) are widely used as impact modifiers in automotive components such as bumpers, and the rise of alternative powertrains, in China in particular, is driving demand for lightweight solutions employing these materials. Simultaneously, competitive priorities are compelling automakers to reduce costs.
A recent collaboration between polypropylene and POE supplier ExxonMobil Chemical and Chinese compounder Kingfa aims to answer these challenges. This collaboration, as well as a collective demand from the automotive industry, enabled ExxonMobil to develop a base resin grade, dubbed Achieve Advanced PP8285E1, which is a high-flow, high-impact copolymer resin designed for automotive applications. Besides realizing the required impact properties with a lower dosage of POE, this grade of Achieve Advanced PP also reportedly eliminates trade-offs in performance, processing, and end-of-life handling compared with traditional polypropylene, unlocking new opportunities for automotive customers.
Using Achieve Advanced PP8285E1, Kingfa created a proprietary formulation that provides a complete solution sought by the automotive value chain, featuring high impact strength, high melt flow rate (MFR), and better odor performance. The improved toughness of Achieve Advanced PP8285E1 helped Kingfa minimize elastomer loading levels to simplify its formulations. It also enabled Kingfa’s customers to produce a variety of tough auto parts — including instrument panels, door panels, consoles, and bumper fascias — more efficiently and economically.
According to ExxonMobil Chemical, Achieve Advanced PP realizes up to 35% higher impact strength versus a standard copolymer, up to 20% improved toughness, and up to 50% less elastomer usage in automotive compounds.
About the Author(s)
You May Also Like