Extrusion basics: Why the compression ratio is like an incomplete forward pass
September 17, 2016
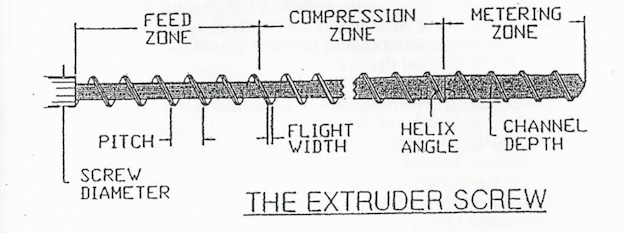
Last month’s article in the extrusion basics series, which dealt with screw design, was very popular (more than 3000 page views!), so I thought I would expand on one of the loose ends—the compression ratio. Here’s the basic diagram again:
The compression ratio of a screw is my favorite way of demonstrating the “disease” of ratiosis and its alternate form, percentitis (inflammation of the percent). Without at least one reference number, ratios and percentages are incomplete and, worse yet, misleading. If I’m driving twice as fast as you are, am I over the speed limit? If I earn 25% less than you for a job, are you paid too much, or are we both underpaid?
Yet we keep defining screws by their compression ratio (CR), usually understood as the ratio of channel depth at feed to channel depth at output. All screws have some compression, partly to make up for the space between the feed particles and, even more important, to make up for the imperfect “bite,” as the feed particles don’t all instantly stick to each other and to the barrel wall. (That’s why grooved barrels feed much better—the grooves keep the particles from sliding around the wall, so the screws don't have to compress as much.)
The depth ratio is technically inaccurate, as compression is three dimensional—the ratio of the volumes of the channels at each end, not just the depths. However, if the diameter and pitch are the same at both ends, the CR is close to the depth ratio (it differs because screw root diameters are not the same). But it’s still a ratio, and, therefore, doesn’t properly and completely describe the screw. For example, if a 3 ½-in. screw has a feed depth of 0.900 in. and an output depth of 0.300 in., the approximate CR would be three. But if another screw for the same machine had a feed depth of 0.450 in. and an output depth of 0.150 in., the CR would still be three!
These two screws would be very different, as the first one would produce much more per turn at a lower level of mixing, while the second one would mix much better but produce less per turn, thus requiring more rpm (if available) and maybe yielding hotter melt. The preference depends on many other things, such as the required torque which might overstress the first screw (thinner root in feed) or the presence of a static mixer in the line or mixing devices on the screw. Material cost even gets into the act: If a screw runs hotter, its effect on degradation can be countered with a more heat-stable formulation, which usually costs more.
Sometimes, special circumstances tell us that we need a higher or lower CR, such as feeding powder or flaky particles, which have a lower bulk factor and thus need more compression, or a rubbery high-friction feed that conveys very well in the feed zone so less compression is needed. The bottom line is that a screw is defined by its actual channel depths along the screw, and especially in the feed and output flights, and not by CR alone. Rear barrel temperatures matter, too, but that’s a topic for another extrusion article in PlasticsToday.
Allan Griff is a veteran extrusion engineer, starting out in tech service for a major resin supplier, and working on his own now for many years, as a consultant, expert witness in law cases, and especially as an educator via webinars and seminars, both public and in-house. He wrote the first practical extrusion book back in the 1960s as well as the Plastics Extrusion Operating Manual, updated almost every year, and available in Spanish and French as well as English. Find out more on his website, www.griffex.com, or e-mail him at [email protected].
In the fall, Griff will present his one-day practical seminar, "Introduction to Extrusion," in Los Angeles on Nov. 15 and Houston on Dec. 5. Topics include the ten (11) key principles of extrusion, plastics chemistry for non-chemists, a review of extrusion hardware, the limits to production rate, quality control of raw materials, simplified rheology, start-up and shut-down procedures and troubleshooting common extrusion problems. E-mail him at the address listed above for more information.
About the Author(s)
You May Also Like