Molding tricks for higher profits, part 5: Cooling the part
It's been said millions of times but many molders don't get it: The mold is the world's most expensive shrink fixture.
March 20, 2017
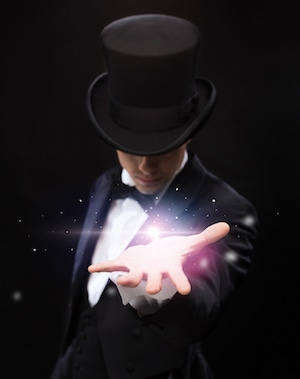
If your original RFQ to the mold builder said, "Design and build a mold to produce part XYZ to print specifications on a 25-second cycle," hold his feet to the fire until that's what you've got! Don't fall for the trick: “We'll process the dimensions in with mold temps and cycle times.” If you raise the mold temp, you extend the cycle. If you lengthen the cycle time, you're using the mold as a shrink fixture. While a second on an eight-cavity mold in a machine running a 20-second cycle at $100/hour machine rate might not seem like much, figure out the profit and machine time you lost in a half million parts! When the part dimensions are out, fix the mold! It is always more profitable than “processing it in.”
Since the mold is supposed to give the part its shape, how cool does it have to be? The common practice is “touchable,” meaning you can pick it up with your hands. But usually the mold has taken way too long to get to this temperature. The scientific answer is 80% of the heat distortion temperature (HDT). Any cooler is a waste of time.
At 80% of the HDT, there will still be thermal shrinkage. There will also be post-mold stress relief shrinkage/distortion. But, it's better to see this distortion sooner than later. I worked on a grille project once. It was twisting, so production left it in the mold longer. Sure enough, when it came out of the mold, it was dead flat but warm. They packed them immediately in boxes and shipped them off. Months later the customer was complaining about warped parts. It turned out the internal heat in the warm parts and the number of grilles packed into the box was enough heat to stress relieve them. Hence, they came out looking like a potato chip. They remolded the parts but this time they had a Lazy Susan shrink fixture allowing a ten-minute air cool while clamped in the proper geometry. Problem solved.
If you set up a simple spreadsheet and look at the cost of shrink fixtures compared with the cost of extended cycle times and capacity you can't use for future jobs, you'll usually see the payoff is very fast and profitable.
Keep in mind you are cooling the melt into a solid state—you are not quenching it! When initially injected into the mold, the plastic molecules are not in their preferred molecular geometry. It takes only microseconds for them to reform into their preferred state while liquid. But if they become solid too quickly, you now have a part with a large amount of internal stress and it will definitely warp.
Even cooling starts with good mold design (as discussed in an earlier article). It requires turbulent flow in the water lines for the best efficiency. This is a matter of consistent setups and temperature control.
But sometimes there are overly thick parts that will “blow out'” when not cooled long enough because the liquid center is still under packing pressure and will soften the outer walls and then bleed out. A good example of this are the electrical insulators used on electric cattle fences. They are made from polypropylene and have some areas that are a half-inch thick! Because of this, my client had a 24-cavity mold built that had to run on a two-minute cycle to avoid the blow-out phenomena. The high cavitation was to offset the slow cycle. I suggested that we cut the cycle to 45 seconds or less. He said he'd tried it with every chiller he had and still got blow out, not to mention brittle parts. The problem here wasn't heat transfer from the steel to the plastic; it was the fact that plastic is a really poor conductor of heat so it takes a long time to come to its 80% HDT to remain stable.
The solution was simple. The blow out showed up about 10 to 15 seconds after the part was ejected. This showed the part initially was structurally cool enough to hold its dimensions until the internal heat warmed it up again. At first, we simply took a 55-gallon drum, filled it full of warm water and ejected the parts into it. Water's heat conductivity is approximately 15 times greater than air. As the internal heat from the part migrated outward, the water absorbed it, keeping the part cool. This evolved into a cattle watering tank, a small propeller mixer and a screen conveyor to offload the parts. With a little tinkering, by the time the parts dropped from the conveyor, they were dry. The heat from the parts kept the water warm, so we didn't do any quenching. At the end of this project, they were molding parts at 29 seconds/cycle and still sealing them at the machine rate with the two-minute cycle!
Sometimes a little extra air-cooling is necessary. We were molding toothbrushes out of cellulose acetate, which is notorious for holding onto its heat. While dimensions aren't terribly important in a toothbrush, in order to put the brush through the bristling equipment it had to be flat and not bent like candy canes. In this case, instead of extending the cycle time, we ejected the parts from the 16-cavity mold down to a slow moving conveyor that went under the press (taking about five minutes) before they landed in a box. We put a hood over the conveyor and then installed a home air conditioner to blow down this tunnel to where the part dropped to slowly cool the parts, having found a simple fan wasn't cool enough.
It's no sin to use shrink fixtures, water baths, cool air or any combination of these to allow the parts to dimensionally stabilize. Sometimes a little hillbilly engineering is the perfect solution.
Tricks when the customer pulls the job
A customer is really buying your expertise, because all your competition has machines, molds and resin. For this reason, don't give it away. Tell your customers, no one is allowed on your production floor for insurance reasons. This keeps your tricks private. When the job goes, keep in touch with the buyer. After a few weeks or months, the buyer will want to give you the job back because nobody can do it as well as you do. Raise the price, re-install your tricks and enjoy the profits. If you must give your customer process conditions do the following:
Shrink fixtures, water baths, and cooling tunnels are cheap. Design, build and pay for them yourself. Since you own them, when the buyer pulls the job don't send them along with the mold. As stated previously, pay for your own mold-mounted water manifolds and balance them. Take them off and ship the mold out with water-line diagrams.
It's your choice.
Bill Tobin is a consultant who teaches seminars and helps clients improve their productivity. He can be contacted at www.wjtassociates.com or via e-mail at [email protected].
Read the previous articles in this series:
"Molding tricks for higher profits: The expert syndrome"
“Molding tricks for higher profits, part 2: The philosophy”
"Molding tricks for higher profits, part 3: The mold"
"Molding tricks for higher profits, part 4: Filling the mold"
About the Author(s)
You May Also Like