Firm Making Concrete Additive from Mixed Plastic Waste Opens First Plant in Australia
The Melbourne facility is Costa Rica–based CRDC Global’s fourth plant worldwide.
April 29, 2024
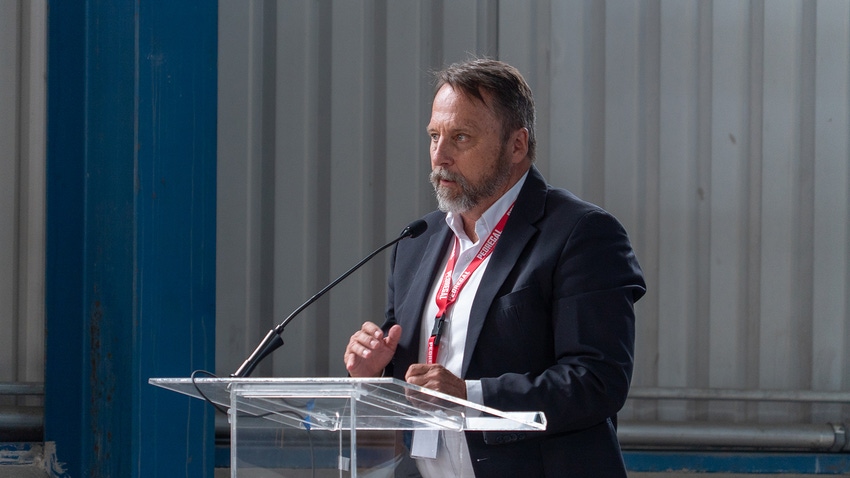
In a significant global expansion, Costa Rica–based CRDC Global Ltd. yesterday opened its first RESIN8 construction materials production facility in Australia. The firm’s patented, low-carbon technology uses shredded, mixed plastic waste as a component to make more sustainable concrete.
Founded six years ago by Canadian native Donald Thomson, CRDC (which initially stood for Center for Regenerative Design & Collaboration) uses a process that accepts any type of plastic waste (resins 1 to 7) and converts it into a range of climate-resilient concrete additives and eco-aggregates, which it markets and produces under the RESIN8 name.
Initial capacity is one tonne/hour.
Located in the Melbourne suburb of Tottenham, the new facility will start with the capacity to process one metric tonne of plastic per hour, but CRDC has ambitious plans to expand this as demand increases.
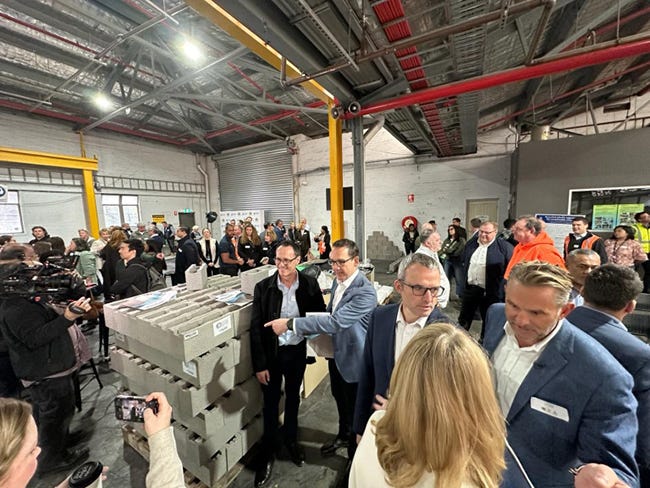
Grand opening of CRDC’s Melbourne plant on April 28. Image courtesy of CRDC Global.
When CRDC first announced its plan last summer to open a RESIN8 plant in Melbourne, it said, “the facility’s modular production lines present ample opportunities for capacity augmentation simply by incorporating additional lines.” This, it noted, aligns seamlessly with the medium-term objectives of the venture, which envisions at least two large-scale RESIN8 plants operating within Melbourne alone.
Stakeholders bear witness to “pivotal” e-waste management moment.
Thomson and more than 100 stakeholders from government, academia, industry, and nonprofits celebrated the plant’s grand opening on April 28. Warren Overton, CEO of the Australia New Zealand Recycling Platform (ANZRP), called the facility’s opening a “pivotal moment” for e-waste management in Australia.
Shane Ramsey, managing director of CRDC Australia, noted that Melbourne is now the fourth city to install a RESIN8 facility. “Thanks to the strong support from ANZRP and the Victorian government, we’re transforming local plastic waste into valuable, eco-friendly building materials right here in our community,” he said during the launch ceremony.
CRDC Global in June 2022 opened the world’s first RESIN8 plant in San Jose, Costa Rica. Later that year it opened its first US facility, in York, PA. It also has launched a plant in Cape Town, South Africa.
Study finds RESIN8 to be viable component in 3D-printed concrete.
Last October, Stellenbosch University in South Africa published a study focusing on RESIN8’s performance in 3D-printed concrete (3DPC). Featured in the Elsevier academic journal Construction and Building Materials, the article spotlights the potential of RESIN8 as a viable component for 3DPC. The research specifically evaluated a RESIN8 mix enriched with elements such as fly ash and a local variety of sand called Malmesbury sand.
University researchers experimented with varying quantities and particle sizes of RESIN8 in the mix. After 3D printing, they rigorously tested these blends for strength, density, and other essential properties.
Additive improves bond strength of printed concrete.
“The most exciting part of the findings,” reported CRDC at the time, “was an improved bond strength between the layers of the printed concrete with the addition of RESIN8. This is particularly significant in 3D printing, where cohesion between layers is paramount. The addition of RESIN8 also enhanced the fluidity of the mix, making it more manageable.”
The study did note that while the mixes containing higher proportions of RESIN8 — up to 15% — met the essential benchmarks for construction, there was a noted trade-off in terms of structural strength. “The good news,” CRDC said, “was that all the mixes still met the requisite benchmarks for construction, cementing their potential in 3D-printing applications.”
Thomson explains that RESIN8 can incorporate all types of discarded plastics from industrial, municipal, and environmental waste streams. The firm shreds the mixed (and often dirty) plastic waste and batches it according to density. It then “pre-conditions” the shredded plastic during a waterless stage that eliminates odors. Next, it melts the resulting mixture during a heated extrusion stage that produces an inert, hybrid mineral polymer. Finally, CRDC granulates the bulk RESIN8 material into the size, shape, and gradation required by specific concrete mix designs.
Independent bodies have tested the material, and CRDC Global says it has been shown to demonstrate an increase in compression strength, flexibility, fire resistance, thermal resistance, and acoustic properties compared with traditional versions. Concrete applications using RESIN8 exceed ASTM standards, and the company claims that the RESIN8 additive is the only material from plastic waste to actually improve the performance of structural concrete products and gain acceptance from the construction industry.
About the Author(s)
You May Also Like