Formlabs Adds a Resin Pumping System and New Materials
Formlabs’ new pumping system and materials were designed to unlock in-house 3D printing in industries from dentistry to industrial manufacturing.
January 12, 2024
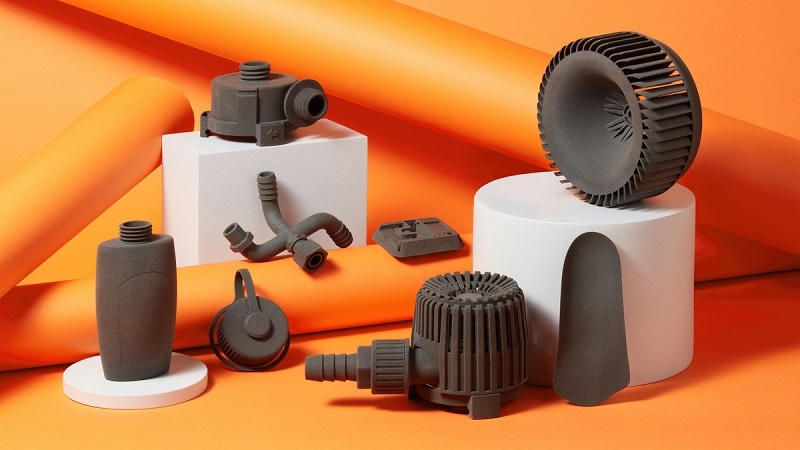
At a Glance
- New 3DP materials
- 3DP pumping system
3D printing company, Formlabs, has introduced a resin pumping system and two new materials, polypropylene powder and premium teeth resin. The goal was to increase the efficiency, versatility, and scalability of its 3D printing ecosystem. Formlabs’ ecosystem supports more than 130,000 printers worldwide.
The resin pumping system and these new materials were developed to bolster in-house 3D printing for a wide range of consumer goods, dental appliances, industrial and automotive parts, and manufacturing prototypes.
The current Formlabs ecosystem includes SLA and SLS 3D printers and more than 45 materials used in-house for prototyping and product design, easing supply chain challenges, producing end-use parts, and rapid tooling. The resin pumping system is Formlabs’ response to increased 3D printing production, designed for unattended printing while lowering cost-per-part and waste.
"3D printing production is steadily increasing, and the introduction of the resin pumping system, polypropylene powder, and premium teeth resin are three big steps in our mission to provide professionals with a full ecosystem of the tools they need to bring their ideas to life.”
Resin Pumping System: Lower Cost Per Part with 86% Less Packaging Waste
As users in more industries add 3D printing into their workflows, the resin pumping system was designed to increase and ease production, lower resin costs, and reduce waste. An accessory for the Form 3 and Form 3L printers, the pumping system is a plug-and-play replacement for standard one-liter cartridges to deliver five liters of resin directly to the printer’s resin tank for continuous printing.
Polypropylene Powder: High-Performance Material
Formlabs notes that polypropylene is the second-most widely produced commodity plastic in the world, commonly used for its low-density, lightweight, and chemically resistant properties for consumer products, packaging, automotive parts, and more. Polypropylene Powder will expand the SLS portfolio, enabling users to print products commonly made of polypropylene, such as home appliances, electronics, sports equipment, custom lab equipment, prototypes, manufacturing tools, and more, efficiently and at a low cost with Fuse 1+ 30W 3D printers.
This video shows some products produced with polypropylene powder:
Premium Teeth Resin: A New FDA Registered Material
Formlabs leads the dental 3D printing industry, with its ecosystem supporting over 15 million dental parts printed. Affordable and accessible 3D printing workflows and specialty materials reduce the cost and labor barriers to dental 3D printing compared to traditional methods, sparking a rise in digital dentistry. Premium Teeth Resin will support 3D-printed denture teeth and temporary full-arch implant-supported restorations (All-on-X) with life-like aesthetics and simplified workflows without compromising on intraoral mechanics.
Premium teeth resin is a nano-ceramic filled FDA-registered Class II biocompatible material with validated longevity that guarantees optimal clinical performance while balancing natural-looking aesthetics. It can be customized to each patient’s anatomy, mimicking natural teeth translucency and opalescence for customizable digital dentures as well as temporary implant-supported restorations. Premium Teeth Resin features industry-leading aesthetics, optimal intraoral mechanical properties, accuracy, and simple workflow to enable affordable yet personal dental care for diverse patient needs.
About the Author(s)
You May Also Like