How medical device OEMs can benefit from glass-filled resins
September 7, 2016
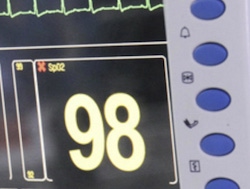
Glass-filled polycarbonate (PC) is playing an increasingly important role in the design and manufacture of today’s medical devices and equipment housings. PC is a proven and well-understood resin, used successfully for many years in medical applications. The addition of glass reinforcement boosts the material’s performance in terms of modulus and strength.
These types of blends have long been known for structural support, durability and compatibility with both powered and passive devices. The material is now also being considered a first choice for applications ranging from handheld surgical instruments to diabetic monitors to insulin pens to equipment housings, where higher stiffness is needed.
In recent years there have been a number of trends driving this move. Consumers and practitioners alike want portability and products with less of an industrial look. OEMs and institutions not only want to keep their customers satisfied but are closely looking at cost. Unlike traditional materials, glass-filled resins provide design flexibility and a more contemporary aesthetic appearance while offering significant cost-saving potential. Following are a couple of ways that glass-filled resins meet these industry needs.
Smaller, thinner parts
Glass-filled plastics can be used to design equipment housings with the same structural support of traditional materials like metal. However, parts can be made smaller and thinner using glass-filled PC, resulting in an overall reduction in weight, which can improve the ease of use of handheld devices and portable equipment. A plastic handle on a surgical instrument will weigh less than its metal counterpart, and it can be designed with an ergonomic grip that gives the surgeon better control.
Available with varying amounts of filler, the material can be used for a variety of applications. Based on end-application objectives and intended functionality, this helps to determine the amount of glass filler that is used. It is important to consider such factors as the pressure or force that will be exerted during a medical procedure, the environment in which the device functions, and the life of the device. Standard flexural stress and flexural modulus tests can be used to determine the strength of the PC with glass fillers and its tendency to bend under load.
Overall, glass-filled resins, because of their rigidity, toughness and dimensional stability, have become a top choice for medical device manufacturers. Structural rigidity, lightweighting potential and design flexibility are key attributes of plastics.
Injection molding simplifies assembly
By using glass-filled plastics, OEMs and molders are able to reap another important benefit: The ability to reduce the number of parts or components in an assembly or application. Instead of having an application with several pieces (think of the traditional steel medical cart with the horizontal and vertical uprights, trays and compartments for small items and handles), OEMs have the opportunity to create a mold that consolidates individual parts into one piece. Imagine going from multiple internal metal components that have to be machined to a simplified design using plastic parts with molded-in features. This not only reduces the cost of manufacturing multiple individual pieces but it can simplify the assembly process, saving time and money. From a final assembly standpoint, it also results in a tighter fit—no gaps caused by misaligned seams, for example—and more robust performance. This can save OEMs the cost of potential reassembly or repair. From a design perspective, it also can provide a cleaner, more contemporary appearance and can even provide a safer device with fewer sharp edges. Design freedom and part reduction are key benefits that can be taken advantage of using glass-filled PC.
Choosing the right glass-filled resin
In an industry that is keenly aware of regulations, OEMs also must be mindful that glass fillers add another level of complexity to the material from biocompatibility, change management and regulatory perspectives. Any changes in the raw material supply chain—whether it’s the result of a new source for raw materials or even an intentional elimination of existing impurities—can impact the material, leading to unforeseen consequences in the end product. Consequently, it is important that OEMs work with material suppliers who are aware of regulatory compliance issues. Medical resin suppliers should carefully assess raw material sourcing and monitor each and every material input and production lot during the life of the medical device.
About the author
Cheryl Weckle is a Development Scientist for Trinseo with more than 27 years of experience in engineering thermoplastics R&D while working at Trinseo and previously at the Dow Chemical Co. She is part of the Technical Service and Development department at Trinseo. For additional information about Trinseo products for medical applications, contact Trinseo at 855 TRINSEO (855/874-6736) or via email at [email protected].
About the Author(s)
You May Also Like