Shepherd Thermoforming & Packaging diverts 43 million water bottles from landfill
Shepherd Thermoforming & Packaging (Brampton, ON, Canada) can provide customers with materials made from up to 100% post-consumer recycled PET water bottles for their packaging needs.
February 14, 2017
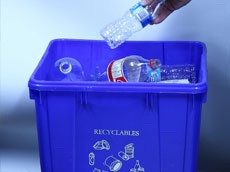
Offering customers the option to use recycled materials is just one benefit that Shepherd Thermoforming & Packaging (Brampton, ON, Canada) provides through its recycled PET (RPET) materials program. They can choose RPET, made from up to 100% post-consumer recycled PET water bottles, for their packaging needs, and contribute to diverting an estimated 43 million water bottles from landfills, according to Mark Shepherd, CFO of the family-owned business. In 2016, the company processed close to four million pounds of RPET.
Shepherd told PlasticsToday in a phone interview that the recycled content varies. “Our suppliers say they can produce 100% recycled material; on average, it ranges from 30 to 60% recycled content,” Shepherd commented.
A few years ago, thermoforming companies that specialized in packaging were experiencing a shortage of RPET. “Sometimes there is a shortage of recycled material and we can only get 30% of recycled PET material. The recycling rates are pretty good here in Ontario, but once in a while it can be a problem.”
PET and RPET is recycled again into new RPET sheet for use in the packaging products the company produces. All other web materials such as HIPS, PP, HMWPE, PVC and ABS are reground and reprocessed into sheet or converted for use in other consumer products such as composite wood decking, vinyl siding and carpeting.
While it is one of the few thermoforming companies that does both thin-gauge forming on inline machines and heavy-gauge forming on two rotary machines, Shepherd said they’re looking to upgrade more in the thin-gauge area. “That’s where we’re seeing the most potential for growth,” said Shepherd, adding that the company’s differentiator is the fact that it is a true custom thermoformer and offers customized packaging design and development.
The company has packaging expertise in a variety of markets including consumer and electronic products, pharmaceuticals, food and confectionary, and medical. The company also provides its customers with advancements in new materials as well as new thermoforming techniques such as contour print forming for food, specialty packaging and consumer markets.
“The food packaging market offers us a lot of opportunity for custom packaging with different features and functionalities, which is our differentiator,” said Shepherd, noting that the company recently received its direct food contact certification (SQF), something that is paying off for the company. “While some companies offer off-the-shelf packaging when it comes to large volumes, we are able to meet demand for large volumes with customized packaging.”
While some food contact packaging requires the use of virgin PET, Shepherd added that “it’s a mix” and that RPET can be a food-approved material for some packaging applications.
About the Author(s)
You May Also Like