The Essential, Sustainable Value of Plastics
How the plastics industry can make plastic work better for the environment.
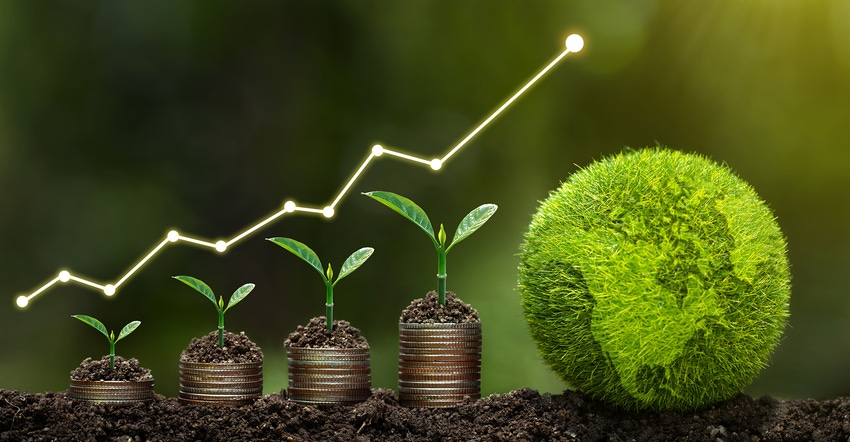
We need a new perspective on plastics. Despite significant pressures to reduce the use of plastics and warnings of its environmental impact, plastics play a vital role in achieving a sustainable world and enabling continued societal advancement.
Next month, the United Nations will host an event to mark the International Day of Awareness on Food Loss and Waste Reduction. As the UN notes, in a world where millions remain hungry, we lose 14% of food produced between harvest and retail, and an estimated 17% of global food production is wasted. In the US, according the Department of Agriculture between 30-40% of the food supply is wasted. When that happens, all the resources used to produce the food — including the water, land, energy, labor, and capital — go to waste. According to the USDA, the disposal of this food loss and waste into landfills contributes significantly to greenhouse gas emissions, with organic waste (such as food) emitting methane as it breaks down – a gas that is 25 times as effective as carbon dioxide at trapping heat in the atmosphere.
Without plastic packaging, food waste would be even greater. Every year in the US, about 30 to 40% of the food we grow goes uneaten, according to the US Department of Agriculture and the American Chemistry Council says that the longer a food item stays fresh, the greater its chance of being eaten. Plastics play a vital role in preserving food and preventing loss. It helps reduce food spoilage by providing a protective barrier and extending the shelf life of food, guarding against light, oxygen, heat, and humidity that can degrade perishable foods and beverages. To take one example, plastic film can increase the shelf life of meat by ten times compared to traditional cutting food waste by 75%. We see similar benefits for a wide range of foods.
Eliminating plastics would add to waste, reduce food security and availability, and contribute to increasing the cost of food – at a time when high inflation across countries is already stretching household budgets.
If we want to feed the world and protect the environment, it’s critical to recognize that plastics must continue to have a place in our food systems even as we work together to minimize the material’s environmental impact.
Plastics waste is a growing problem.
The goal here is never to downplay the well-founded environmental concerns surrounding plastic waste. Plastic waste has doubled in the last two decades and is set to triple again by 2060. According to the OECD, globally, only 9% of plastic waste is recycled. The rest is incinerated (19%), dumped in uncontrolled sites (22%), or ends up in regulated landfills (50%).
Faced with a growing problem, governments have begun to act. In 2002, Bangladesh became the first country to ban thin plastic bags, reflecting their role in clogging drainage systems and causing or exacerbating flooding. By 2021, the European Union had banned single-use plastic plates, cutlery, and more as well as cups, food and beverage containers made of expanded polystyrene, and all products made of oxo-degradable plastic.
Most recently, California signed SB 54 into law last year. It’s a bill that by 2032 will require all packaging in the state to be compostable or recyclable. It also requires that by 2032 100% of packaging in the State of California be recyclable or compostable, 25% of plastic packaging be cut, and 65% of all single-use plastic packaging be recycled.
As California’s new law recognizes, reducing plastics is only one part of the solution. Plastics will still be essential not just to protect food but also for various other uses, including pharmaceuticals for packaging pills, medical devices and filtration, and critical medical supply infrastructure.
Moreover, alternatives are not necessarily better for the environment. Plastic is also often lighter than other options, for instance, which means less fuel and lower greenhouse gas emissions to transport it. One study calculated that replacing plastic packaging in Europe with alternatives would boost packaging mass by a factor 3.6 and increase GHG 2.7 times – by 61 million tonnes of CO2. Indeed, plastic’s light weight is the reason it’s a key material in the manufacture of electric vehicles, where it’s used in place of metal to reduce mass and power requirements. As the push for increasing electrification continues, we can expect plastics usage to increase dramatically.
We need to reduce plastic packaging, but also recycle more of it. As noted in California SB-54, the legislation also requires that 65% of all single-use plastic packaging be recycled by 2032.
A workaround that can revolutionize recycling.
Recycling, just like reduction, has its own challenges, however.
Regulations for recycled plastic used in packaging food and medicines are rightly strict as many materials are simply unsuitable for traditional mechanical recycling infrastructures.
Mechanical recycling shreds or crushes plastic waste and then melts it to be reused but doesn’t significantly change the chemical structure. This can be used for PET to make drink bottles — PET is by far the most common plastic that is mechanically recycled.
Other types, however, cannot be processed this way. For instance, thermoset plastics are made of polymers that form irreversible chemical bonds, which cannot be recycled. Cling film is an obvious example. With collection, sorting and processing usually unable to adequately separate different types of plastic waste, less than 10% of plastic waste ends up being recycled.
Since critical properties of mechanically recycled plastics are too compromised for use in food packaging, virgin material derived from fossil sources is typically required. However, there may be a workaround.
Honeywell’s UpCycle Process Technology employs an industry-leading molecular conversion, pyrolysis, and contaminants management technology to convert waste plastic to Honeywell Recycled Polymer Feedstock. This can then be used to create new plastics. And it can do so repeatedly, breaking down waste plastic into its molecular building blocks to create a recycled polymer oil (RPO) that can be used to create new, virgin-quality plastic, closing the circularity loop even for food-grade plastics to both alleviate the plastic waste issue without losing the positive impact plastic affords our food supply chains.
Crucially, the UpCycle Process Technology expands the types of plastics that can be recycled to include colored, flexible, and multilayered packaging, as well as polystyrene — waste that would otherwise go unrecycled.
When used in conjunction with other chemical and mechanical recycling processes — along with improvements to collection and sorting — Honeywell's UpCycle Process Technology has the potential to help recycle nearly 90% of waste plastics. This would represent a considerable increase in the amount of waste plastics that can be turned into polymer feedstock.
It could be a critical technology in our move towards a circular economy, where we continue to reap the benefit of plastics for protecting food and other uses — without costing the earth.
Marc Yagoub is a Global Business Director within the Honeywell Sustainable Technology Solutions Group. He works at Honeywell UOP Ltd, United Kingdom, where he’s accountable for the Advanced Plastics Recycling portfolio with special focus on closing the plastics circularity gap and driving value for Users.
His full profile is found on LinkedIn.
About the Author(s)
You May Also Like