Safety on the plant floor should be job 1
Plastics processor Bixby International has made the creation of a safe working environment its top priority. CEO Dan Rocconi shares the experience and its rewards with PlasticsToday.
December 12, 2016
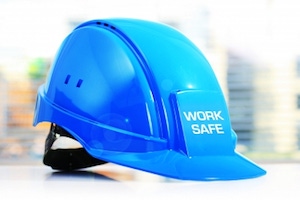
When it comes to safety on the plant floor, no company can let its guard down. As Bixby International, a custom thermoplastic sheet extruder and laminator for the thermoforming industry, said in a recent newsletter, “A factory floor does not always provide a perfectly safe environment for workers.” Bixby’s plant in Newburyport, MA, like many plastics processing plants, has a lot of equipment that “rely on heat and intense pressure” to make its products.
Image courtesy fantasista/ |
That’s one reason the company has made it a primary management initiative to make Bixby’s plant safer, starting at the top with Bixby CEO Dan Rocconi. Rocconi came to Bixby from chemicals giant DuPont, a company known throughout the industry for creating the safest environment possible for its workers. One of the first things Rocconi did was to bring in a safety consultant to get an outsider’s viewpoint of Bixby’s plant floor.
Rocconi explained to PlasticsToday that the consultant was extremely helpful because an outside individual provides a fresh set of eyes. “He came in, started walking the production floor and interviewed employees about procedures,” said Rocconi. “He found a number of upgrades we could make, such as machine guarding, tripping hazards and some general housekeeping items. He also went through our procedures such as lock-out/tag-out, which is important but sometimes can be neglected.
“It’s easy to look at a machine or piece of equipment and say nothing is going to happen—I’ll just leave it for 10 minutes. Having clear procedures and making sure people follow them is important, particularly in areas such as lock-out/tag-out because it’s not part of a daily routine.”
In addition to some basic issues that were resolved such as machine guarding, tripping hazards and other typical plant floor hazards, employees came through with other safety suggestions regarding procedures such as cleaning out pieces of equipment that Bixby had gotten blind to. “That fresh set of eyes really helps,” said Rocconi.
Creating a safe working environment also involves getting input from employees, who work closely with the machinery and equipment every day. Members of the management team go onto the plant floor to hear directly from employees about what needs to be done to ensure a safe working environment. The company also holds quarterly town hall meetings for each shift—Bixby is a three-shift operation—to address any issues and provide safety training. “Once the employees learned how much management cared about creating a safe work environment, the recommendations came flooding in,” said Rocconi, noting that the company has 54 employees.
Most company managers dread a visit from OSHA (Occupational Safety and Health Administration), but Bixby took its dedication to creating a safe work environment a step higher and called the local office of OSHA, inviting officials in on numerous occasions to conduct safety audits, which have also proven to be extremely helpful. “There were still a few things they found that we had to work on, particularly around machine guarding or some of the older ancillary pieces of equipment that weren’t properly guarded, but overall we’ve been doing really well over the past few years,” said Rocconi.
“We have a safety committee and track everything on a spread sheet, and take suggestions from people on the floor, which was the most useful thing we did.”
Employees are not the only beneficiaries of the safe work environment at Bixby—so are its customers. The company has found that safe employees are more focused and do better work, which ensures better products for customers. Having a safe environment also helps Bixby to control costs. After hearing about Bixby’s safety program, other companies have asked about it in a desire to emulate it. “Bixby is proud to set a good example across the plastics industry as a company that does all that it can to create a culture of safety throughout its organization,” said Rocconi.
When asked to provide our readers with the three most important things plastics processors can do to create a safe work environment, Rocconi said:
Get information from the people on the floor doing the work and provide a way for them to bubble-up ideas up to make things safer. Get that voice!
Get an outsider to come in and evaluate your plant. An outsider is not blind to things that we see every day and don’t notice.
Plastics processing machinery tends to have a lot of “nip points” that employees can get their fingers or hands caught in. It’s very important to understand how to use this machinery and how to make it safer.
Through this experience Bixby has learned that safety is a journey, not a destination, which is why the company is constantly trying to improve the work environment. To accomplish this, Bixby continues to conduct audits, and encourages and accepts suggestions from employees. Moreover, Bixby collects as much data as possible on “near misses.” Information like this is very useful in trying to identify unsafe conditions, he said. However, the reason for these “near misses” is that Bixby’s ongoing safety program has reduced the number of accidents to only one or two per year. With numbers this low it is hard to find trends, leaving Bixby no option but to analyze “near misses,” said the company.
Rocconi speaks to Bixby’s commitment to safety this way: “Safety has to come from the top. If I lose my focus on safety, it will not be long before we start to slip as an organization. Fortunately, I have a great team here and they are not shy about reminding me of the importance of safety. When your employees are comfortable enough to call you out on safety, you know you have a strong safety culture.”
About the Author(s)
You May Also Like