In spite of the extensive use of robots and automation on the factory floor, the lack of skilled employees remains one of the biggest concerns in manufacturing.
June 5, 2018
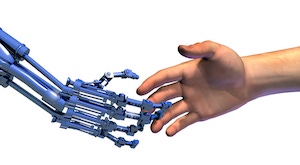
Robots and other forms of automation will massively hurt the U.S. workforce. That’s what I typically read in some of the more pessimistic headlines and what I just read in a study of Industry 4.0 that I wrote about here, but is it true? That blanket statement isn’t new and has been a dire prediction since robotics and automation came into use in the 1980s.
The gloom-and-doom scenario has mostly proven to be a myth, given that the unemployment rate currently is at 3.8%. With 5% unemployment considered by economists to be full employment, it’s no wonder that manufacturers are having a tough time finding people to fill open jobs. The good news is that 18,000 new manufacturing jobs were added in May, according to the Bureau of Labor Statistics, most of them in durable goods manufacturing.
The Institute for Supply Management’s report on manufacturing for May, released on June 1, shows the Purchasing Management Index for employment up 2.1% in May to 56.3% from April’s rate of 54.2%. Only automotive had a lackluster month, with jobs in that industry down 4,400.
While that doesn’t sound good, the industry continues its constant search for skilled workers, especially among the Tier 1 supply base, as the Original Equipment Supplier Association’s quarterly report shows.
Back in the 1980s when robotics was coming into play in a big way on automotive manufacturing production floors, unions anticipated an end to humans working in that industry. New contracts with the then Big 3 automakers contained clauses that limited the number of robots allowed, and ensured workers would retain their jobs in spite of automation.
Today, despite the extensive use of robots and automation on the factory floor, the lack of skilled employees remains one of the biggest concerns in manufacturing. That fact alone makes the idea of putting a tax on robots—something that has been proposed in certain areas of the country—a rather ludicrous idea. If manufacturing employers can’t find workers today with all the robots in action on the factory floor, reducing the number of robots through taxation will only make matters worse.
Most employers say that robots and automation, including the networking and digitization of Industry 4.0, will free up human labor for more value-added work.
Some economists note that robots will be an absolute necessity as baby boomers retire in full force over the next 10 years, the overall population shrinks as people have fewer children and the types of jobs available in manufacturing shift to what millennials prefer—high-value jobs that require the skills Industry 4.0 demands.
I don’t think that today’s manufacturing worker has much to fear from the Industry 4.0 wave. There will be challenges across the board, but savvy processors and mold manufacturers will be able to incorporate their workforce into the new digitized, networked manufacturing plant without too much angst.
About the Author(s)
You May Also Like