Milacron closes 2017 with double-digit sales growth and strong cash flow from operations
For the full year, Milacron achieved 9% order and 5% sales growth and, despite numerous inflationary headwinds, continued to expand EBITDA margins with a 20 basis point improvement.
February 21, 2018
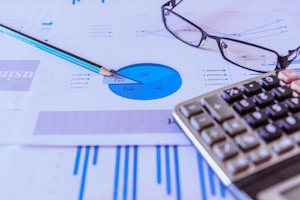
Milacron Holdings Corp. (Blue Ash, OH) closed out 2017 with a strong fourth quarter and exceeded its full-year sales, adjusted EBITDA and free cash flow guidance ranges. That was the message delivered by Milacron President and CEO Tom Goeke at a press conference held Feb. 20. “We delivered nearly double-digit constant currency sales growth in the quarter, driven by our APPT (Advanced Plastic Processing Technology) segment with 16% sales growth, and our Fluid Technology segment grew five percent on a constant currency basis,” stated Goeke.
For the full year, Milacron achieved 9% order and 5% sales growth on a constant currency basis and, despite numerous inflationary headwinds, continued to expand EBITDA margins with a 20 basis point improvement. “We also delivered significant free cash-flow improvement, as our focus on lowering working capital provided exceptional results to the quarter and full year,” Goeke added.
“Full year sales of $1.2 billion represented a 5% increase versus the prior year. The consumables portion of our portfolio had another strong performance with 8% growth, and moves the consumables mix to 64% of total sales,” Goeke continued. “Our hot runner and fluids businesses were exceptional performers in 2017. Our Mold-Master grew double digits, led by growth in China.”
Milacron completed the China facility expansion in 2017, and the company will continue to expand its machining and assembly capacity in 2018 to keep up with global hot-runner demand. The fluids business had a record year, noted Goeke, delivering mid single-digit growth in all regions and over 22% EBITDA margins. “We are hitting our stride, and I remain bullish on the business and the team’s ability to execute,” he said.
Looking ahead to 2018, Goeke said Milacron began the year with a “strong backlog position of $287.0 million. “We are focused on concluding our three-year restructuring initiatives and will continue to take the necessary actions to meaningfully strengthen our balance sheet,” he stated. “Our guidance for 2018 reflects the continued execution of our strategic fundamentals, which include driving increased sales from consumables, expanding margins in all of our businesses and increasing free cash flow conversion to position our company for growth.”
The aftermarket portion of Milacron’s equipment business grew 5% in 2017, as the company’s aftermarket investments continued to “gain traction,” Goeke said. “Our India business delivered another impressive year with double-digit top-line growth. Like our China-based hot-runner business, our India manufacturing facility is undergoing another round of expansion to keep up with market demand.”
Milacron CFO Bruce Chalmers noted that “growth in our core business is focused on consumables growth and leveraging our expansions and continued investment in China and India.”
With NPE coming soon, Goeke mentioned that Milacron will release a new product at that international trade show taking place in May. The only headwinds that Milacron encountered with pricing during 2017 were in North America. With contract being a “large segment” of Milacron’s North American business, the most significant price pressure came from automotive, where there are large contracts with molders. “Fifty percent of our total price pressure came from that one segment—automotive—with larger tonnage injection molding,” Goeke stated.
Goeke noted that the company decided to “walk away” from a “chunk”
of that business [large-tonnage presses for automotive] “which saw $30 million in orders last year. I expect we’ll have the similar in the first half of this year,” he said. Milacron plans to “aggressively” get back into that market with a “different performance and different cost structure” in the large-tonnage press range.
“We’ve gone back to the drawing board in the case of performance and cost on a new product line, which we’ll release in Q2 and Q3, obviously taking orders in Q3 and Q4,” he added. “The balance of the market is relatively healthy.
“So, I think we’ll see a little less headwind from pricing in 2018 due to the fact that we have been able to say ‘no’ in a few segments on a few orders that were really interesting.”
Let’s do the numbers
For the fourth quarter of 2017, sales of $324.0 million increased 12.4% from sales of $289.1 million in the same period a year ago. Excluding the favorable effects of currency movements, sales for the fourth quarter increased 0.9% versus the prior year period. Operating earnings for the fourth quarter increased 14.8% to $10.1 million compared to $8.8 million in the same period a year ago.
Adjusted EBITDA for the fourth quarter of 2017 increased 12.7% to $60.4 million, or 18.6% of sales, compared to adjusted EBITDA of $53.6 million, or 18.5% of sales in the prior year period. Net earnings totaled $3.3 million, or $0.05 per basic and diluted share, in the fourth quarter of 2017 compared to a net earnings of $1.1 million, or $0.02 per basic and diluted share, in the prior year period. Adjusted net income totaled $42.0 million in the fourth quarter of 2017 compared to adjusted net income of $32.8 million in the prior year period.
For the full year ended December 31, 2017, sales of $1,234.2 million increased 5.8% from sales of $1,166.7 million in the prior year. Excluding the favorable effects of currency movements, sales for the year ended Dec. 31, 2017, rose 5.2% over the prior year. Operating earnings for the year ended Dec. 31, 2017, decreased 16.7% to $88.0 million compared to operating earnings of $105.6 million in the prior year, being negatively impacted by $9.7 million of incremental restructuring costs when compared to the prior year.
Adjusted EBITDA for the year ended Dec. 31, 2017, increased 6.8% to $227.3 million, or 18.4% of sales, compared to adjusted EBITDA of $212.8 million, or 18.2% of sales in the prior year. Net earnings totaled $1.1 million, or $0.02 per basic and diluted share for the year ended Dec. 31, 2017, compared to net earnings of $30.5 million, or $0.45 and $0.32 per basic and diluted share, respectively, in the prior year. Adjusted net income totaled $128.2 million for the year ended Dec. 31, 2017, compared to adjusted net income of $105.7 million in the prior year.
Due to the impact of the Tax Cuts and Jobs Act of 2017, Milacron recorded a net income tax benefit of $8.9 million, or $0.12 diluted adjusted earnings per share. This benefit was primarily driven by the release of valuation allowances on the company’s AMT credits and the revaluation of net deferred tax liabilities, partially offset by the recognition of withholding tax liabilities on planned cash repatriation from non-U.S. subsidiaries.
Sales in Milacron’s Melt Delivery & Control Systems (MDCS) for the fourth quarter of 2017 were $103.6 million compared to $101.0 million in the same period a year ago. Excluding $3.7 million of favorable effects of currency movements, sales decreased 1.1% compared to the prior year period. For the year ended Dec. 31, 2017, sales were $423.9 million, an increase of 8.7% compared to sales of $389.9 million in the same period a year ago.
Milacron’s 2018 outlook is positive. In line with current market conditions, Milacron forecasts 2 to 4% sales growth in 2018, which is inclusive of an anticipated 1% foreign currency tailwind. Adjusted EBITDA is forecast to be between $237 million and $243 million. Free cash flow is forecast to be between $80 million and $90 million.
About the Author(s)
You May Also Like