May 31, 2018
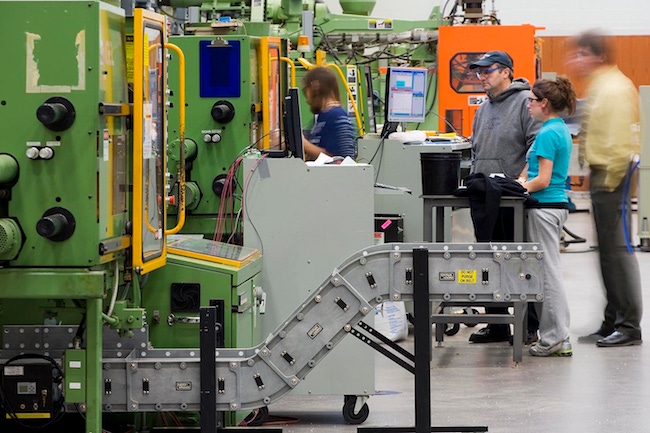
Construction of the Shell cracker plant in Beaver, PA, as of November 2017. Image courtesy Shell Chemical. |
Having never been to Pittsburgh, I wasn’t sure what to expect when the Pennsylvania Department of Community and Economic Development invited me and a handful of other journalists on a press trip last month. I knew that the city’s steel- and coal-fueled past, which brought prosperity but at a considerable human and environmental cost, was a dim memory. I didn’t have a notion of what the city and environs looked like today or if there was a blueprint for the future. By the end of a whirlwind three-day tour visiting businesses and universities and conversing with local and regional officials, it was clear to me that the best may be yet to come for Pittsburgh and, indeed, western Pennsylvania. Part of that future is being built in Beaver, a few miles northwest of Pittsburgh, where Shell Chemical is constructing a massive $6 billion ethylene cracker plant that taps into the Marcellus shale formation. Alongside that project, a concerted effort by public officials, industrial leaders and academic institutions to promote advanced manufacturing and energy innovation is also leading the way to a cleaner, brighter future.
Sharing the shale
Pennsylvania, Ohio and West Virginia all own a piece of the Marcellus and Uttica shales that hold massive deposits of oil and natural gas. The governors of those states have formed the Tri-State Shale Coalition to develop a petrochemical hub that can compete with the Gulf Coast. Inevitably, there is competition among the neighboring states to lure investment dollars, but the breadth of the shale reserves argue for a more collaborative approach, according to the coalition.
Noting that the natural resource doesn’t stay within state lines, “we don’t want to be competing with each other,” said Denise Brinley, Senior Energy Adviser for the Pennsylvania Department of Community and Economic Development. “Our biggest competitor is the Gulf Coast, not neighboring states.” Still, Pennsylvania has pulled ahead in the regional race, with Royal Dutch Shell investing $6 billion to build the ethane cracker. Ohio may be nipping at its heels: There are reports that PTT Global Chemical is considering building a cracker plant there that would call for a $10 billion investment.
A key objective of the regional partners is to parlay the cracker plants and gas extraction into infrastructure improvements, regional job creation and off-shoot investments. In fact, the Beaver project is projected to have a five- to seven-time multiplier effect on associated business activity, according to Brinley.
“With regard to natural gas liquids (and ethane, in particular), we are currently exporting 100% of our ethane to other domestic and international markets and that won’t likely change until Shell Pennsylvania Chemicals comes on line in 2021-2022. This project represents the first in-state use of ethane, and we have a compelling economic case if the resource is both extracted and used as close to the source as possible. We want to encourage other 'Shell-like' projects to consider this region for investment because of that strong value proposition,” said Brinley.
A study conducted by Shell determined that 70% of its potential North American polyethylene customers lie within a 700-mile radius of the Beaver site. Moreover, unlike the Gulf Coast, the region has no disruptive hurricane season. Those factors have kept the project on track, even when oil prices took a dip. When all is said and done, the plant will have created approximately 6,000 construction jobs and 600 permanent jobs.
Downstream demand
The plastics industry already has a strong foothold in the region, notably the so-called Plastics Cluster in Erie County and northwest Pennsylvania. Companies well-known to the PlasticsToday community, such as Micro Mold/Plastikos, Silgan Plastics and Berry Plastics, have a decades-long presence in the area.
Advanced polymers producer Covestro, known as Bayer MaterialScience until Bayer spun out the business in September 2015, has been a high-profile presence in the Pittsburgh area for many years. Its expansive facility sits alongside the Bayer plant.
And near the airport, GE opened its $39-million Center for Additive Technology Advancement (CATA) in 2016. A year later, GE announced that it was developing the CATA into an externally focused Customer Experience Center. Equipped with an array of industrial additive manufacturing equipment, the center enables clients to glimpse the potential of 3D printing under real-life conditions.
Penn State Behrend's Plastics Engineering Technology program is one of only six such programs recognized by the Engineering Technology Accreditation Commission. Image courtesy Penn State Behrend. |
A third pillar of the region’s advanced manufacturing framework is a supportive educational ecosystem. For the plastics industry, that begins with Penn State Behrend: Its Plastics Engineering Technology (PLET) program is one of only six such programs recognized by the Engineering Technology Accreditation Commission. The university's plastics processing laboratory is the largest undergraduate educational facility of its type, housing millions of dollars’ worth of computers, materials, and processing equipment.
With its high density of plastics manufacturers creating downstream demand for ethylene and an engaged academic environment, the “Erie region is uniquely positioned to take advantage of this opportunity,” according to Amy Bridger, Senior Director of Corporate Strategy and External Engagement at Penn State Behrend. “Our plastics companies are well established and positioned for growth. Expansion of the Plastics Engineering Technology program at Penn State Behrend and the development of new curricula and research will help those companies and others across the industry meet the workforce demands of a larger, Pennsylvania-focused market,” Bridger told PlasticsToday. “Our students also will benefit, through opportunities for industry research, increased exposure to potential employers and the sort of experiential learning that you can’t offer in a classroom.”
As it stands, 63% of PLET graduates are still living in Pennsylvania, according to the school. If all goes according to plan, even more graduates will have fewer reasons to leave the region in the years ahead.
About the Author(s)
You May Also Like