The Challenges of 3D Printing in a Regulated Industry
Medical 3D printing must reckon with regulatory guidelines, which prioritize consistent, stable processes.
September 27, 2023
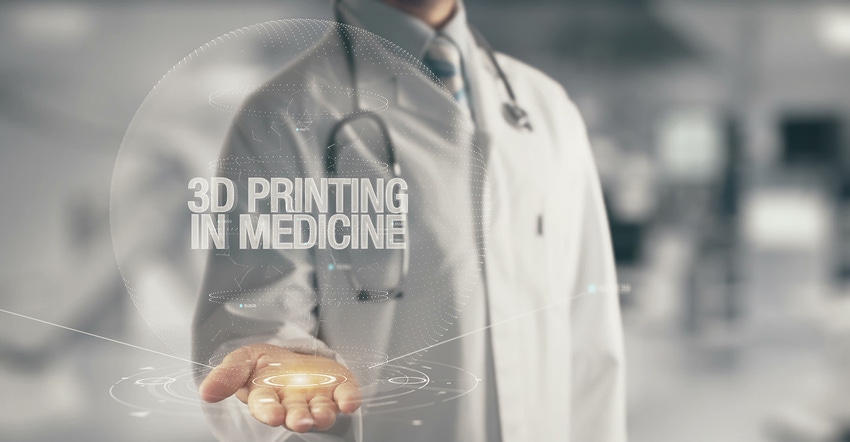
3D printing’s greatest strength in the medical space may also be its greatest handicap. The rapid design and fabrication of unique patient-specific medical devices made possible by the technology must comply with regulatory guidelines, which are typically predicated on repeatable, consistent processes. A panel of experts versed in medical 3D printing at Advanced Manufacturing Minneapolis in October will discuss the ramifications of regulatory guidance in the United States and European Union (EU), along with the promise and limitations of the technology. Perry Parendo, who has 18 years of medical device consulting and training under his belt, will moderate the panel discussion. He spoke with PlasticsToday about the benefits 3D printing brings to the medical space for both patients and practitioners and the role that government guidance can play to ensure product safety, consistency, and quality.
EU regulations lack clarity
FDA has a slight edge over the EU’s fairly new Medical Device Regulations (MDR) when it comes to establishing 3D printing guidelines in medical device applications, according to Parendo, president of Perry’s Solutions LLC. “The FDA provided formal guidance for 3D printing in 2017. As with any guidance, it is comprehensive for all possible medical device applications. This means not every area is needed for each device. It is up to the user to figure this out, which is a challenge. As we gain experience with approvals and audits, things will get clarified,” Parendo told PlasticsToday.
By contrast, the EU’s MDR lacks clarity regarding 3D printing while raising the bar in terms of general device expectations, said Parendo. “The regulations are confusing regarding what constitutes a custom device. Some say EU MDR is a more challenging area than handling the FDA expectations for 3D printing.”
The session at the Minneapolis event, which includes co-locates Plastec and Medical Design & Manufacturing (MD&M), will address the commonalities and differences of both systems through the lived professional experience of the panelists.
Keeping pace with 3D printing breakthroughs
The importance of medical device regulations keeping pace with the ground-breaking advances of 3D printing without overreaching and creating unnecessary obstacles cannot be overstated. “The ability to 3D print parts has massive impact on orthopedic applications and similar unique body areas,” noted Parendo. “Without the need for special tooling, the lead time for these parts can be greatly reduced, and the part geometry can be far more complex than would be possible using conventional technologies, which can allow for smaller volumes.”
The panelists have individual expertise in hearing aid, dental, and orthopedic applications. “These are unique areas of the human body, and benefit from the flexibility of 3D printing. However, the full range of applications is yet to be seen,” added Parendo. One application that was presented at last year’s event in Minneapolis illustrates the far-reaching impact of 3D printing in the medical field.
Separation of conjoined twins
“The University of Minnesota presented a case involving the separation of conjoined twins,” recalled Parendo. “An MRI of the internal organs for each twin was available, but the team went further. They created a 3D model for each twin’s organs with different colors. This allowed the surgical team to practice the procedure and visualize what was going to happen during the separation. The ability to mimic reality created a change in the surgical strategy and ensured efficiency. Training medical staff and medical device users by means of 3D printed parts brings us far beyond the previous scope of prototyping R&D components. The panel this year likely will bring its own game-changing examples,” said Parendo.
As a relatively new technology, compared with injection molding, for example, 3D printing also currently has limitations. They tend to revolve around available materials, according to Parendo.
A question of consistency
“For example, the 3D printing material may not match the properties of a final injection molded part,” explained Parendo. “With a stable process and stable product in conventional manufacturing, we can gain experience and be confident in our overall consistency. If the final medical device is truly unique and the final product is produced with 3D printing, how do we know the process is consistent? The nature of a flexible product begs the question of knowing everything is stable. It is a new set of questions to answer,” said Parendo.
Surface finish and file transfer protocols are also problematic in a regulated industry such as medical manufacturing. “Surface finish variation can have an impact on part performance, so new secondary operations create another area of interest and the need for stability. This requires extra process development and qualification. While it is not hard, it is something new,” said Parendo.
File transfer also poses some problems, according to Parendo. “Moving from concept to the 3D printer can use several file formats to obtain the final product. This is an area of FDA concern, and we need to be aware of stability and consistency, since each 3D-printed product can be unique.” One example he cited resides in having confidence that radius features are recognized during the file transfer process. “The ability to verify initial design intent and the final product features is an important aspect that provides traceability value for the manufacturer and for audit.”
Unleashing the full potential of medical 3D printing
By sharing their real-life experiences in a range of applications, the panelists will provide attendees with the confidence to bring 3D printing deeper into their industries, said Parendo. Recognizing that new regulations and uncertainty may restrain users from exploring the full potential of 3D printing, Parendo also feels, however, that the “medical space can be assertive.” He strongly believes that the FDA and EU want industry to expand the use of 3D printing. “They simply want industry and users to be aware of areas of interest to ensure patient safety. Understand and address those areas, and regulatory agencies will be on board.”
All of this and more will take the form of a lively discussion at Advanced Manufacturing Minneapolis, which returns to the Minneapolis Convention Center on Oct. 10 and 11, 2023. The panelists taking part in the conversation include Nathan Alt, director of regulatory affairs and quality assurance at Formlabs; Wes Gentry, principal manufacturing engineer at Starkey; and Greg Voss, quality systems director in the Office of Advanced Manufacturing at the Veterans Health Administration.
Advanced Manufacturing Minneapolis, which includes co-located trade shows devoted to plastics processing, medical design and manufacturing, packaging, and automation, features more than 500 exhibitors. The conference running alongside the exhibition has scheduled dozens of educational sessions in addition to the panel discussion on medical 3D printing. A complete schedule is available online.
Advanced Manufacturing Minneapolis is organized by Informa Markets – Engineering, which also publishes PlasticsToday.
About the Author(s)
You May Also Like