Clariant making its additives fit for reuse
Halogen-free flame retardant allows re- and up-cycling of PA6, 66; Exolit OP 1400 maintains UL 94 V-0 rating after recycling of production waste as verified by Fraunhofer LBF institute.
September 12, 2019
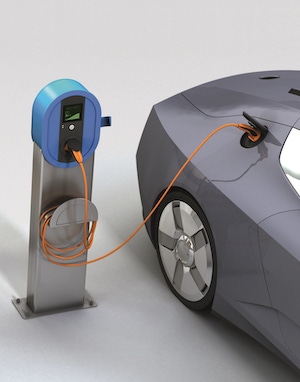
Clariant is working to improve its additives, making them fit for re-use while avoiding material performance degradation. A showcase of this is the recycling and upcycling of flame-retardant polyamide (PA) post-industrial waste. Research institute Fraunhofer LBF confirms that PA6 and PA 66 engineering plastics containing Clariant’s halogen-free flame retardant Exolit OP maintain their UL 94 V-0 rating also when recycled back into production streams multiple times. This is advantageous both for the environment and manufacturers who are keen to increase their use of production waste and post-use recyclate in electrical, electronic and automotive applications.
Halogen-free flame retardant allows re- and up-cycling of PA6, 66. |
Even under the assumption that plastics could be re-designed to a large extent to better fit to recycling, contaminants and additives may be accumulated in the material over several mechanical recycling cycles, and this may lead to poor performance or even health risks. Being phosphorus-based and halogen-free, choosing Exolit OP as a flame retardant is a safer and an environmentally superior option compared to legacy brominated flame retardants. Its use is even more relevant considering the rise in demand for PA66 engineering plastics, pushed by industry trends such as miniaturization in E&E, the shift to more lightweight materials in automotive and by rising mobility demand.
Electric vehicles have their specific material and safety requirements. Because of the high energy content of the battery and the high voltages and currents employed, not only flammability is a risk, but also electrical arcing, which can in turn lead to a fire. This risk is addressed by measuring the current tracking index (CTI) where short circuiting on a surface is mimicked. In this test, Exolit OP phosphinates perform exceptionally well. Furthermore, the “signal orange” color for high voltage parts can be a challenge to achieve and maintain, in particular for polyamides, in harsh under-the-hood conditions.
Confirmation from the Fraunhofer LBF Institute over a multi-year research collaboration with pinfa (the Phosphorus, Inorganic and Nitrogen Flame Retardants Association) that Exolit OP continues to deliver the same high-level fire protection throughout many recycling and reuse cycles is a further boost. Post-industrial waste of glass fiber-reinforced PA containing Exolit OP provides manufacturers with a genuine alternative to new material. Additives can ensure that mechanical performance is also not affected, meaning that internally recycled waste or regrind material can be used to produce the same applications without the need to downcycle. Test results were published (here).
In addition, Exolit OP is not subject to ecodesign application restrictions, for example the upcoming EcoDesign regulation for electronic displays based on the EcoDesign Directive (2009/125/EC) covering the recycling of plastics, which limits the use of halogenated flame retardants in enclosures and stands of electronic displays.
Stephan Lynen, Head of BU Additives, Clariant comments: “Global e-waste is estimated at approx. 50 million tonnes annually. of which only 20% are effectively recycled. At Clariant we are dedicated to ensuring our additives are not part of that waste. Take automobiles, one of the most recyclable engineered products, offering recovery rates of up to 90%. As the industry shifts towards a circular economy, any contribution we make to recyclable plastics that improves automotive waste management will support OEMs in selecting lighter weight and sustainable materials. With Exolit OP, OEMs can be confident of a flame retarded PA for their application which is recyclable and safe.”
About the Author(s)
You May Also Like