Pyrowave Announces First Finished Products Using 100% Recycled Styrene
Test results from Michelin and Knauf Industries in France reportedly show properties and performance are identical to virgin fossil-sourced styrene.
September 14, 2023
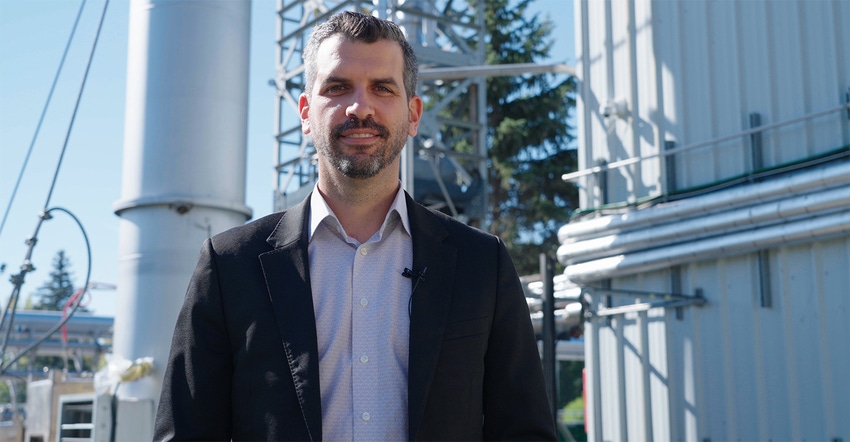
Montréal-based Pyrowave said this week that it has reached a new milestone with its microwave-based depolymerization technology — the first finished products made from its 100% recycled styrene. Michelin and Knauf Industries in France have successfully produced batches of finished elastomer and plastic products incorporating plastic waste recycled in Canada using Pyrowave technology. Tests reportedly show that the properties and performance of elastomers made from recycled styrene were identical to materials made from virgin fossil-sourced materials.
Michelin to incorporate recycled styrene in tires
Michelin has produced a four-ton prototype batch of styrene-butadiene rubber (SBR) at its plant in Bassens, France, according to Pyrowave. The SBR produced using 100% recycled styrene passed all quality tests, an important milestone for further tests incorporating the recycled styrene in tires for laboratory and track applications, said Pyrowave.
Material complies with food-contact regulations
Knauf Industries, a supplier of expanded polystyrene (EPS) packaging, technical parts, and insulation products, generated expanded polystyrene parts via Knauf Circular using Pyrowave’s recycled styrene. The resulting products also passed all lab tests demonstrating equivalency with products made with fossil-based virgin styrene. Migration tests confirmed that the material was suitable for food-contact applications.
The tests performed by Michelin, which has been collaborating with Pyrowave since 2020, and Knauf Industries incorporating recycled styrene are significant as SBR and EPS are technical polymers used in the industry, explained Pyrowave. Since SBR and EPS production processes are relatively sensitive to contamination, the success of these tests demonstrates the reliability of Pyrowave technology and that the recycled styrene can replace fossil styrene in technical applications while improving a product’s environmental footprint. The technology reduces greenhouse gas emissions by 82% according to a recent life-cycle analysis commissioned by Pyrowave, and allows waste plastics to be used as a raw material, furthering the goals of a circular economy.
Seamless integration in entire value chain
“Pyrowave's technology has already reached an industrial scale and undergone extensive piloting over the past decade,” President and CEO Jocelyn Doucet told PlasticsToday. “Its primary application focuses on depolymerizing polystyrene, transforming it into valuable styrene monomer. Today's announcement underscores that our solution seamlessly integrates into the entire value chain, offering exceptional quality, robustness, and commercial viability. It also highlights our commitment to collaborative partnerships throughout the value chain,” said Doucet.
Using microwave technology to disassemble polymers into their constituent parts has several advantages over traditional thermal-based advanced recycling processes that rely mostly on fuel-based heating of polymers, according to Doucet.
Pyrowave’s technology enables rapid and high-intensity heating, resulting in an impressive yield of nearly 100% liquid products in the output, said Doucet. “In contrast, conventional thermal-based processes have slower heating rates and consequently yield only about half the Pyrowave output. This translates to higher productivity and improved economics when harnessing microwave technology. Moreover, the energy efficiency of microwave-based processes allows for the use of renewable energy sources, a pivotal step toward decarbonizing the chemical industry,” Doucet told PlasticsToday.
About the Author(s)
You May Also Like