New Production Tracker Streamlines Data Collection
At NPE2024, Wintriss Controls Group will demo its system that tracks a range of inputs with minimal operator involvement.
April 12, 2024
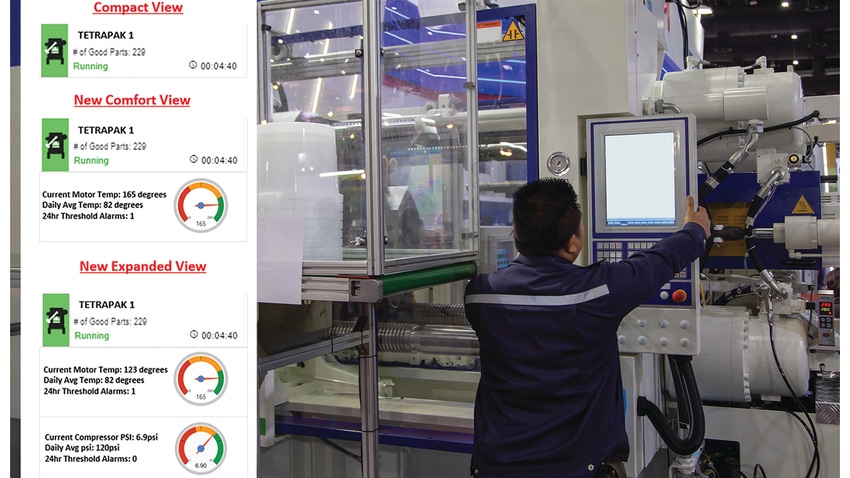
New production tracking hardware from Wintriss Controls Group will be demonstrated at NPE2024 alongside advanced features of the company’s ShopFloorConnect software.
The New Wintriss ShopFloorTracker (SFT) device makes data collection easier with less operator involvement, thanks to preprogrammed digital inputs to capture and track process parameters including run/idle and counting. Analog inputs include temperature, pressure, flow, voltage, and electrical current.
Device collects temp and pressure data.
Injection molding operations especially benefit from the temperature and pressure data collected by the device — and that data is viewable in different formats according to operator preference.
“We are excited to introduce ShopFloorTracker at NPE2024,” said Keith Magnant, general manager of Wintriss Controls Group. “Based on customer feedback for a re-imagined, easy-to-use hardware solution for tracking a range of inputs, we developed the new device so that unique machine data is automatically sent to ShopFloorConnect software.”
Multiple machines tracked.
ShopFloorTracker is designed to work with the company’s Wintriss SMI 2 monitoring hardware interface to track multiple machines. In a production department using the SMI 2 and ShopFloorConnect (SFC) software, a ShopFloorTracker can be added to each machine. The 3-x-6-x-1-inch device can have a temperature sensor connected to one analog input and a pressure sensor in another. The SFT then connects wirelessly to SFC to begin data collection.
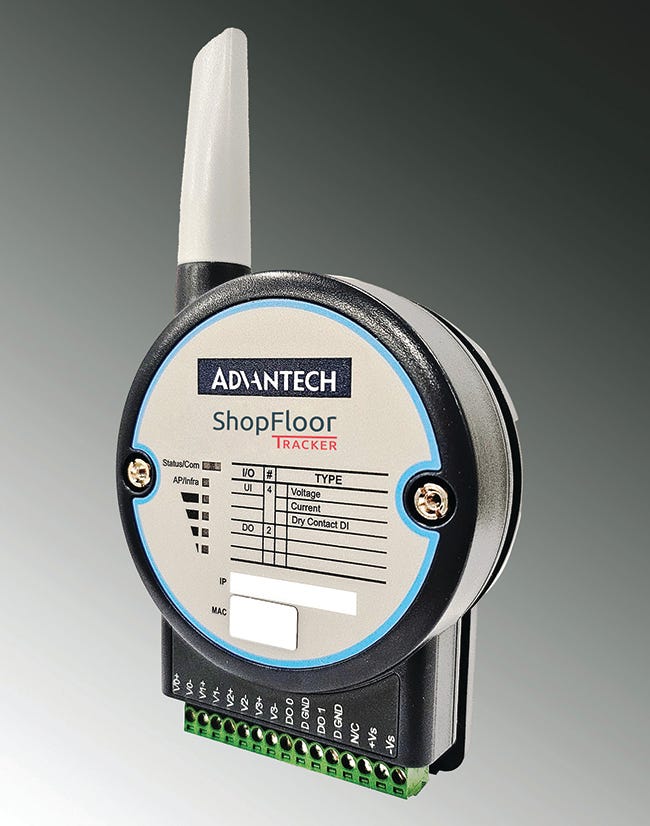
The ShopFloorTracker works with a monitoring hardware interface to track multiple machines. Image courtesy of Wintriss Controls Group.
The SFC software collects data that is “timely, accurate, and unbiased,” the company noted, with real-time displays, programmable alerts, powerful reporting software, and browser-based operation. To measure overall equipment effectiveness, SFC analyzes machine utilization, downtime, and production rates to improve productivity and cost savings across a wide range of machines.
Meanwhile, the SMI 2 features 32 fully customizable downtime codes and comes network ready and factory preconfigured. “Forced Dialog” mode can inhibit machine restart until a reason for downtime has been sent to SFC. Operator number, job number, and a job identifier can be entered for each job on the 6.5-inch color touchscreen. The interface is available either in an enclosure or for panel mounting.
Visit Wintriss at booth S22211 at NPE2024 at the Orange County Convention Center in Orlando, FL, from May 6 to 10.
About the Author(s)
You May Also Like