Plastikos expands automation capabilities, eyes further growth
Customer demand to further diversify into new materials, technology, and manufacturing capability has provided the opportunity for Micro Mold and Plastikos Inc., Erie, PA-based mold manufacturer and custom injection molding company, to invest $500,000 towards expanding automation capabilities.
October 21, 2015
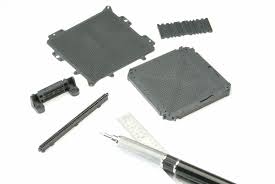
Recently, Plastikos was awarded a program from a large global Medical Device OEM who develops Enteral Feeding Systems (among other devices). The finished component consists of rigid substrate material that is later over-molded with flexible thermoplastic polyurethane (TPU). The TPU material acts as a sealant whenever the device is not in use.
The operation is heavily automated to support the yearly demand on the finished device. A high-speed robotic center was custom designed to properly load the rigid substrate into the second multi-cavity tool, unload the finished over-molded component, and monitor shot-to-shot consistency throughout the injection molding process. The tool is fully equipped with cavity pressure transducers that are integrated into the robotic work center. This way, individual cavities can be automatically sorted/scrapped in the event of a potential non-conformance.
“The real challenge was ensuring all elements of the supply chain were communicating effectively with one another,” said Rob Cooney, Plastikos’ Manufacturing Manager. “We needed to make sure that the robot would fit within the space limitations of the molding machine and complete all phases of loading and unloading and detection sequence.”
Over the last year, Plastikos has installed automation and robotic centers throughout the facility. “We are continuing to look at ways to automate our manufacturing-related process, such as packaging, inspection, raw material and finished product handling, and so on,” Cooney said. “This new automated manufacturing cell should open the door to other exciting opportunities.”
Plastikos’ top management also built a sizable clean room assembly area within the Company’s larger ISO class 7 clean room. The Company also purchased two additional medical molding machines in August—88 tons and 220 tons. Both machines are fully integrated with 3-axis robots and end-of-arm tooling capabilities, cavity pressure monitoring systems, advanced process monitoring software, integrated hot runner systems and mold-protect vision systems, as well as integrated into Plastikos’ corporate IQMS ERP system. The Medical Division expansion was completed in June of this year, and is built to house eight molding machines with dedicated quality, tool room, mold vault and office space.
Philip Katen, President of Plastikos commented: “We continue to see a growing need from our medical customer base to take on more advanced manufacturing and component assembly work that expands beyond our precision tool making and injection molding service offerings. Our clean room assembly area within our brand new Medical Expansion will likely be dedicated towards a range of secondary operations such as ultra-sonic welding, custom labeling, and other value-added operations.”
About the Author(s)
You May Also Like