Extrusion basics: Let’s talk garbage
Is bad resin to blame for contaminated product? Here’s how to find out.
March 19, 2018
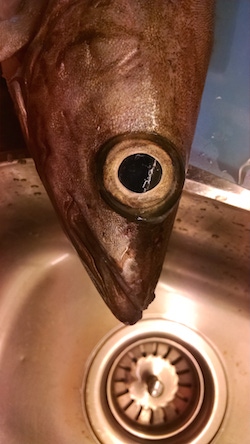
Yes, I’m reminding you again that there are no toxic plastics, and we are the missionaries that must convey this true gospel to the masses. This is a gospel with scientific validity, so why doesn’t everyone believe it? Send your comments to me at [email protected] or talk to me in person at the NPE/ANTEC by calling my cell phone before, during and after, at 301/758-7788.
My extrusion topic this month is garbage. Not trash, a word we may use to avoid the dirtier word, garbage, but also a word with many other meanings. Garbage is stuff we don’t want and can’t use. We especially don’t want it in our products. People who can’t say the word “garbage” may have the handicap (at least in a factory) of delicacy.
Why a fish? Read on—all will be revealed. |
Whodunit? As a tech service engineer for a major resin supplier, I had the delicate task of trying to show that we didn’t do it, that it didn’t come in with the resin, that we were clean but something—or someone—else was at fault. And we had to make our case to people who wanted to pin the tail on us, so they could get a refund or resupply or some other atonement for our errors.
Wadizzit? Our defensive tactics included questions, a microscope, some knowledge of the material and extrusion conditions and sometimes the inside of the melt pathway. Also time. Even if you are in a rush, never show it, as that exposes weakness, and you may accept some responsibility just because of your time stress. Follow the three Ps: Patience, politeness and persistence.
Questions include asking for samples of the contaminated product and, if possible, samples of the resin used to make it, along with ID (product, lot and container numbers); how and when it was delivered; and any tests done on the resin before it was used. (See my column from October 2015, which dealt with testing of incoming resin.)
Sometimes it was possible to show that our resin couldn’t have been the problem, because it was delivered after the problem was first seen, or the particle size and shape weren’t ours (strands versus pellets, for example).
Offer to run a sample in a lab extruder. I say offer, because you may never have to do it. If the “plaintiff” thinks it might not be us, but we are the deep pockets that want to keep the customer, he may accuse us even with no technical evidence, which is the next thing we should ask for.
Now use the microscope. I was strongly encouraged to take an elective course in microscopy in college. We thought the push was from the professor who wrote the textbook and wanted to sell more of them—I bought mine used from an older student—but the course turned out to be very useful. We learned that differences in mineral form reflected the atomic arrangement, learned how to identify various fibers (including paper and synthetic) and how curly hair differed from straight. To this day, I carry a little magnifier when I visit a factory.
In an extrusion, I would be looking for color, clumping of smaller particles, round versus irregular contours and fibrous nature. You don’t need an expensive high-powered microscope either—a 50 to 100x pocket scope is enough.
If the particles are black and borders are irregular, it may be highly degraded plastic, usually from slower-moving or dead spots in the head and die (including the screw tip). Look at the screens: If it’s made in the screw, fragments may be caught on the screens. If the screens are clear, “cooking” places are in the head and die. Causes include overheating or running too slowly, which would increase the time-temperature product that relates to degradation. Don’t forget that materials are not all equal in terms of thermal stability; some can resist more time-temperature before discoloring. For more stability, you can add more antioxidant (stabilizer for PVC) like a colorant concentrate, buy a more stable resin or run cooler melt. Also, starting a clean system with a super-stabilized material prolongs the period before degradation sets in.
The lab extruder can be very helpful here. It is usually small enough that, if started clean, it will not develop degradation in the short time needed to test. If the first extrudate comes out clean, then it’s likely the bad stuff is being made in the product line. If it is bad from the beginning, it’s a sign that maybe it did come in with the resin. But not always. Anyone who’s afraid to be double-checked should be. There is a legendary case of a processor in New Jersey who found black specks in his Texas-made resin, complained, and was surprised to learn that the specks were insect fragments from flies that lived in a nearby pasture of a species unknown in Texas. Some happened to fly into the silos where the resin was stored and laid their eggs.
Round or other smooth-edge particles are usually classic gels, sometimes called fisheyes (hence, the image that accompanies this article)—resin crosslinked by the heat and, thus, unable to melt in with the truly thermoplastic mass. Some fluoresce in UV light. They may be clear or yellowish/brown, and are soft enough to distort and get through some screens, or else break up into gel showers (sprays of little gels). If fine screens don’t do the job or raise back pressure high enough to overheat the melt, try sintered-metal filter disks or any of the extended-area filter devices common in the textile industry.
Fibers are rarely a continuous problem, and easy to deal with once diagnosed. Paper may be from bags opened over the hopper, or napkins and notes tossed into scrap bins that are not covered and clearly marked for recycle. And do recycle all the scrap and trim that you can, and keep the containers covered. Remember ULS-FOS-TANA = Use Less Stuff, Fix Old Stuff, and Throw Almost Nothing Away.
Allan Griff is a veteran extrusion engineer, starting out in tech service for a major resin supplier, and working on his own now for many years as a consultant, expert witness in law cases and especially as an educator via webinars and seminars, both public and in-house. He wrote the first practical extrusion book back in the 1960s as well as the Plastics Extrusion Operating Manual, updated almost every year, and available in Spanish and French as well as English. Find out more on his website, www.griffex.com, or e-mail him at [email protected].
Griff will present a live seminar in Atlanta, GA, on April 12 and in Amherst, MA, on May 22. Seminars in your plant are also available. If you can’t attend his live events, he offers a Virtual Seminar, which can be seen at any time, anywhere. E-mail Griff at the address listed above for more information.
About the Author(s)
You May Also Like