Kudos for composites: Innovative formwork debuts in new Uyllander bridge
Building bridges over busy waterways tends to be accompanied by delays and disruptions to shipping traffic. Installing the steel structure, building the wooden formwork for casting the concrete deck, erecting the falseworks to support the formwork, dismantling the falsework and formwork after the concrete has hardened - all of these activities will unavoidably inconvenience or even block the normal passage of ships and barges on the canal or river.
March 12, 2014
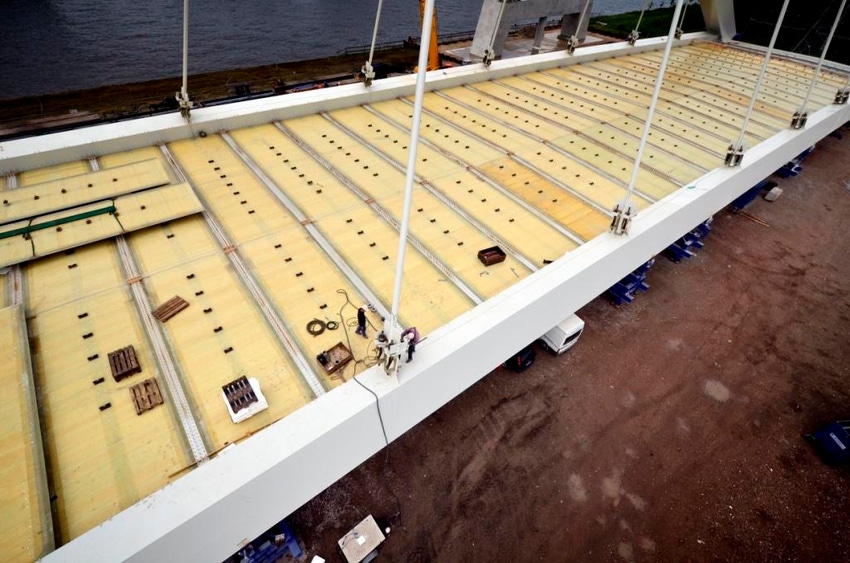
Building bridges over busy waterways tends to be accompanied by delays and disruptions to shipping traffic. Installing the steel structure, building the wooden formwork for casting the concrete deck, erecting the falseworks to support the formwork, dismantling the falsework and formwork after the concrete has hardened - all of these activities will unavoidably inconvenience or even block the normal passage of ships and barges on the canal or river.
The engineers building the Uyllander bridge in Amsterdam, which spans the busy Amsterdam-Rhine Canal, an important shipping artery connecting the port of Amsterdam to the Rhine River, therefore decided to try something new.
Rather than moving the steel structure into place and then building the formwork, they turned the process around. The structure - a steel arch and steel trusses spaced 3.8 meters apart - was constructed on shore, after which a lightweight, polymer sandwich-panel formwork was installed, also on shore.
It's the first time composite sandwich materials have been used in this way. Poly Products, in Werkendam (Netherlands) was entrusted with the task of designing and manufacturing the panels which would meet the requirements of a low weight and high stiffness and strength, respectively. According to Albert ten Busschen, technical director at Poly Products, two requirements played a dominant role in the design of the panels. In the first place, the deflection in the middle of the panel could not be more than 25 mm when the concrete is cast (weight of concrete and accompanying steel reinforcement: 800 kg/m2). This meant using a sandwich structure to obtain the necessary stiffness. The second major design challenge was the fact that the upper part of the panel resting on the truss was not allowed to protrude more than 20 mm above the steel flanges of the supporting steel sub-structure. Limiting the support thickness at the edges in this way meant that a supporting edge was needed. A supporting edge with a thickness of 15 mm was engineered that was mounted on a 5-mm thick rubber strip.
Based on various simulations, calculations and analyses, the laminate build-up was determined, and test panels were constructed which underwent stringent testing to determine whether the panels complied with the prevailing design codes for composite materials and - importantly - whether the two design requirements had been satisfactorily met. In other words: were they up to the task of supporting the concrete casting?
When this proved to be the case, Poly Products went on to produce the 72 glass fiber reinforced panels needed for the bridge via vacuum assisted RTM technology, complete with the integrated holes needed for installing the steel strips to hold the pipes running under the bridge.
The panels were installed on shore, after which the bridge was moved into place, the steel rebar was constructed and the concrete deck was cast.
To compensate for the deflection of the panels when the concrete was poured, ten Busschen noted that "in production the panels were made with an upward arch of 25 mm so that after casting the concrete the panels will become practically flat at the bottom side. This is done in view of aesthetics."
Talking to Jeroen van der Vlis of Poly Products about the project, he observed that the advantages of using composite sandwich panels for the formwork turned out to be many. "Everything was lightweight and prefab, which meant quick and easy installation. The interruptions to traffic were minimal, which was the whole point. Plus, composite materials are hardy and weatherproof. And they could be left in place - no costly dismantlement needed."
He added: "Because of their smooth under side, they required no further finishing and will require very little, if any, maintenance in the future."
The bridge is currently in the final stages of construction and will open later this year. It was designed by Wim Quist of Quist Wintermans Architekten, in collaboration with Ingenieurs Bureau Amsterdam (IBA). Due to the unique application of a permanent composite formwork, it has already attracted much attention from the industry, garnering various innovation prize nominations and an innovation award since 2013.
About the Author(s)
You May Also Like