Innovative UHMWPE braiding technology opens new avenues in medical device design
A new automated braiding technique paired with ultra-high molecular weight polyethylene (UHWPE) fibers has the potential to improve device design for minimally invasive procedures.
November 10, 2017
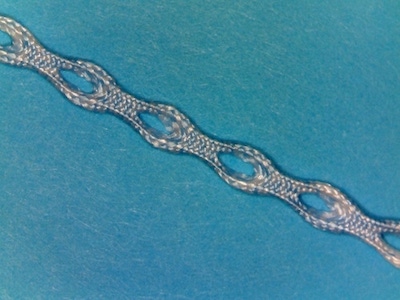
A new automated braiding technology developed by Meister & Cie AG (Hasle-Rüegsau, Switzerland) using ultra-high molecular weight polyethylene (UHMWPE) fibers from DSM Biomedical (Heerlen, Netherlands) has the potential to advance design options for medical devices used in minimally invasive surgery (MIS). The patented technology—Implantable Holding Device (WO2017/0167)—paired with high-strength, low-profile UHMWPE Dyneema Purity fibers reportedly improves interfacing of textiles to other medical device components and reduces the amount of metal required in the device, thus improving patient outcomes.
A branched textile structure. |
MIS has been adopted globally in operating rooms, as the technique has been proven to reduce pain and accelerate patient recovery following surgery. The technique requires not only small instruments but also small, flexible and/or foldable expandable implants, write Philippe Gédet, Engineer, Meister & Cie AG, and Lavinia Panella, Senior Applications Development/Technical Support, DSM Biomedical, in a just-published white paper.
“There is a general trend toward implants made partly or completely of textiles,” explain Gédet and Panella. “During the design and development phase of such new implants, it is essential to address the future need of interfacing textile with either hard and soft tissue or an additional metal device component. Today, knotting, splicing or sewing are options often seen as the solution for this interface. However, all three solutions can be manufactured only through manual or semi-manual processes.” Meister, a developer of technical textile braided products and manufacturing partner of DSM Biomedical, has developed an automated continuous process to replace the manual process in the production of loop-like braided structures using medical-grade UHMWPE fibers. The benefits, according to the white paper, include increased throughput and repeatability as well as greater strength retention in the material.
As explained in the white paper, the automated braiding technology allows each bobbin carrier to be guided through individual paths, making it possible to achieve a branch-like structure resembling an eyelet (see image above). Each branch structure represents a tubular braid. The technology enables control of the individual paths as well as the per inch cross (PIC) counts of the different braided sections. This opens up many new design options, according to Meister, which tested the platform using variable fiber grades in a range of dimensions.
Example of the fixation concept applied to ligament reconstruction. |
For the unbranched portions as well as the two legs after the first branch, Meister successfully achieved highly reproducible textile constructions at resolutions down to 0.5 mm using Dyneema Purity SGX 55 and SGX 110 dtex fibers. “For example, an eyelet could have a length of 2.5 mm—five times that of 0.5 mm—and the unbranched structure in between could measure 4 mm, eight times that of 0.5 mm,” write Gédet and Panella.
The platform technology has specific applications in sports medicine (ACL reconstruction, for example), orthopedic and spinal procedures. For additional technical information, download the free white paper.
About the Author(s)
You May Also Like