Molder stops sweating small stuff thanks to automation
Converting the insertion of 0.4-mm-diameter, 1.65-mm-long parts into slides with injection cavities that are barely larger than the part from a manual to automated process proved daunting. A combination of vibratory feeding, vacuum suction and robotics achieved success.
July 11, 2018
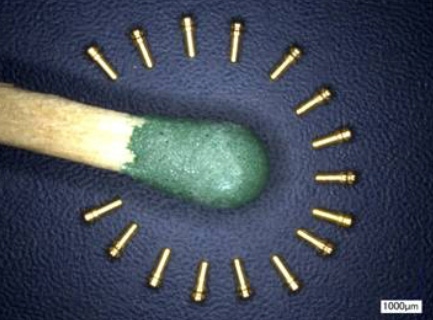
When injection molding and toolmaking company Reiter HG Geiger Kunststofftechnik GmbH (Hilpoltstein, Germany) sought to automate a delicate, precise assembly process, finding a partner proved to be daunting. The operation, which was being done manually, involved the insertion of 0.4-mm-diameter parts measuring 1.65 mm long into slides with injection cavities that are barely larger than the parts. Several companies Reiter approached did not consider their technology up to the task, given the miniaturization of the components and the precision required in their manipulation. It began to seem like the “task was not even solvable,” said Process Engineer Hans Kolb, but perseverance eventually paid off. A mechanical engineering firm partnered with Reiter to develop the right combination of vibratory feeding, vacuum suction and robotics to automate the process.
Contacts, including pins less than 1 mm long, must be placed in a slide for overmolding. |
Reiter produces a thermoplastic part with overmolded contacts for a medical application. Slides with two injection cavities each hold four metal components. Manually inserting the tiny parts into the slides, which have a clearance of less than 0.01 mm, requires extreme concentration and poses a major challenge for consistent product quality. "In addition, the work as a whole is rather monotonous, which makes it hard to stay focused," said Kolb. Another disadvantage of the manual loading method is that if the surface coating is damaged, the parts are unusable.
Orders for the parts were steadily increasing, making it feasible to consider automating part of this process. After a rigorous and sometimes frustrating search, Reiter HG Geiger Kunststofftechnik GmbH partnered with a mechanical engineering specialist to develop a system that reliably separates and grips the pins and positions them in the slides.
The first hurdle in automating the process involved separating the contact pins for the subsequent pick-and-place operation. This was achieved with the use of a grooved vibratory bowl that feeds the part to a vacuum-based suction device. A robotic arm grips the pin and brings it to the slide.
Another challenge encountered by the engineers was ensuring accurate insertion of the pin in the tool cavity. Similar to the injection molding process, the slide is initially centred in the robotic cell with the aid of short-stroke cylinders and is then clamped to stop it from slipping. Each carrier is coded individually so that it can be identified by the system. "This is necessary because not all tool slides and holes can be made exactly the same in the 0.01-mm range,” said Kolb. “So that the robot finds the appropriate holes, it is specially trained on each slide. This allows the pin to be properly positioned, inserted and returned immediately.”
The entire process comprising four pins per slide takes only a few seconds. The fully assembled change-over slide is placed in the injection molding machine after a visual inspection and overmolding begins while the finished parts are removed from the previous slide and checked. The empty carrier is returned to the cell for refilling, resulting in a seamless cycle. In addition, the machine performs the same task with a time delay to feed a second injection molding workstation on the other side of the machine.
Since all the complex processes in the system are pre-programmed and run autonomously, it was very easy for the staff at Reiter to get used to working with the new robotic colleague, said the company. All components such as sensors, actuators and controllers communicate via Profibus and ensure that the robot follows the defined movement steps.
The process itself is directly controlled by inserting or removing the slides: A green light indicates that a slide on one side is fully populated. As the worker removes the slide and inserts an empty one, the robotic arm is busy with another slide on the other side. If the opening is accessed when the green light has not been activated, the robot stops immediately. The same thing happens if the large front door is opened, for example, to refill pins in the hopper.
Throughput is roughly the same as when assembly was performed manually, but more importantly, said Kolb, employees have been relieved of the strenuous handling of the extremely small inserts and error rates have declined. "Based on these good experiences, an expansion of the range of applications is conceivable. The machine is ready,” added Kolb: The initial design left space for two more slide feeders.
About the Author(s)
You May Also Like