Eco-based TPVs target cradle-to-cradle applications
Based on its Keltan Eco—the world’s first bio-based EPDM rubber—Arlanxeo (Maastricht, Netherlands) has formulated TPVs using sustainable ingredients. Potential partnership opportunities are available.
July 6, 2018
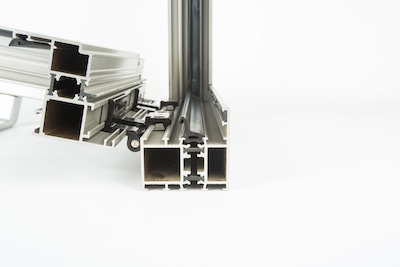
Performance elastomers supplier Arlanxeo (Maastricht, Netherlands) has introduced thermoplastic vulcanizates (TPVs) that combine Keltan Eco ethylene propylene diene monomer rubber (EPDM) with green fillers, plasticizers and thermoplastics, resulting in EPDM products with up to 90% sustainable ingredients.
Window profiles for buildings is one application targeted by eco TPV grades. |
Keltan Eco is the world’s first EPDM rubber manufactured using bio-based ethylene extracted from sugarcane. Depending on the ethylene content of each rubber grade, the proportion of bio-based material ranges between 50% and 70%.
After evaluating the potential of creating sustainable alternatives for traditional polyolefin thermoplastics, plasticizer oils and (reinforcing) fillers, Arlanxeo has developed thermoset rubber compounds and TPVs based on Keltan Eco EPDM with the specific aim of maximizing sustainable content without compromising technical performance.
By combining Keltan Eco EPDM with green compounding ingredients, the new EPDM compounds can also be used for dynamic and static automotive sealing applications with 85–90 weight percent of its composition having sustainable origin and a technical performance comparable to standard EPDM compounds.
Niels van der Aar, Business Development Manager EPDM/NBR at Arlanxeo, said: “We can now identify potential partners to (co-)develop these innovative bio-TPVs. TPVs using Keltan Eco EPDM offer an excellent opportunity to replace regular thermoset rubber compounds and thermoplastic vulcanizates. These bio-based TPVs can make a significant contribution to the circular economy, scoring well in a cradle-to-cradle approach and helping to lower the carbon footprint.”
Studies have shown that both the characteristics and technical performance of these Keltan Eco EPDM grades are identical to those of conventional EPDMs produced via Ziegler Natta catalysis and/or those from monomers based on crude oil.
Today, these new bio-based EPDM grades are commercially tested and used in applications, such as window profiles for buses and buildings, automotive extrusion profiles, O-rings, TPV over-moldings for automotive interiors and pharma applications, sport surfaces and, most recently, in the sponge rubber layer directly underneath the outer cover of the official soccer ball of the 2018 FIFA World Cup.
About the Author(s)
You May Also Like