NPE Visitors Get Sneak Peek at PEK
Polyplastics’ new polyetherketone (PEK) resin reportedly is more heat-resistant than PEEK, making it a prime candidate for metal replacement in harsh environments.
April 10, 2024
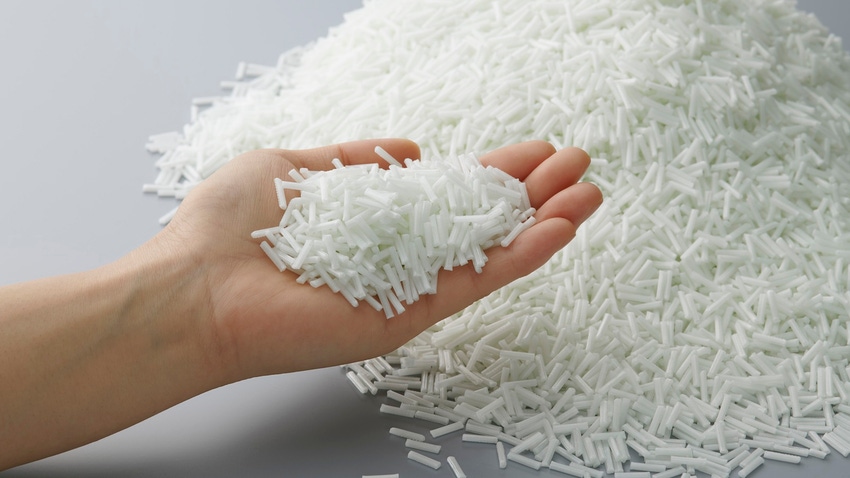
Engineering thermoplastics supplier Polyplastics will showcase its latest material technologies, including the launch of a new polyetherketone (PEK) resin, at NPE2024 next month. The company is exhibiting in booth S26207 from May 6 to 10 at the Orange County Convention Center in Orlando, FL.
The company also will offer an update on its other resin offerings including polyacetal (POM), polyphenylene sulfide (PPS), liquid crystal polymer (LCP), polybutylene terephthalate (PBT), and cyclic olefin copolymer (COC), along with long-fiber thermoplastics (LFT), and demonstrate how they meet the requirements of the automotive, electronics, medical, and packaging industries as well as expectations for environmental sustainability.
Polyplastics will introduce to its line-up Sarpek PEK, an advanced material for metal replacement and applications requiring the highest heat resistance of any injection moldable resin without post-curing.
Better than PEEK
Sarpek PEK is an engineering plastic positioned at the top of Polyplastics’ portfolio of crystalline polymers. It is an advancement over polyetheretherketone (PEEK) that delivers a high crystallization rate and molding efficiency. Sarpek PEK also features higher heat resistance than PEEK, with sufficient durability and strength to replace metals in harsh environments, where other crystalline plastics fail and metals are heavy and noisy.
Sarpek PEK has a melting point of 370°C and glass transition temperature of 155°C. It is available in unreinforced grades along with 30% glass-filled and 30% carbon-fiber-filled grades.
PPS for EVs and hybrids
Polyplastics also will showcase Durafide PPS 6150T73, the company’s latest offering for the electric vehicle (EV) segment. The high-performance material delivers heat resistance and thermal and electric insulation properties for busbars, module covers, and battery systems in electric and hybrid (xEV) vehicles. The material significantly improves thermal and electric insulation properties during thermal runaway without the use of heavy inorganic insulative sheet structures. It maintains the insulation properties of busbars and module covers even after exposure to environments of 1,000°C for 30 minutes.
Additionally, Polyplastics announced global availability of its Laperos LCP materials. With full acquisition by Daicel in 2020, Polyplastics has expanded its options for growth and geographical market coverage. The company has extended LCP sales to EMEA and the Americas while making timely investments in capacity to better respond to market growth.
Sustainable automotive composites
As part of the presentation of its sustainability initiatives, Polyplastics will highlight the availability of Plastron LFT, a long cellulose fiber-reinforced polypropylene (PP) resin, which is being targeted for automotive applications such as door module carriers, center consoles, and armrest cores. The eco-friendly Plastron LFT, which is made of specially formulated regenerated cellulose fibers, provides weight reduction plus mechanical strength, enabling manufacturers to reduce their carbon footprint and meet today’s sustainability demands.
Eco-friendly resins that incorporate natural fibers, starch, wood powder, and other plant-based and natural mineral filler materials are being considered for use in a broader range of applications. Cellulose is a promising material to help reduce CO2 emissions, but low strength is a limiting factor. Polyplastics has addressed this problem by using regenerated cellulose in the development of LFT resins with an excellent balance of physical properties. Plastron LFT offers lower density and reduced greenhouse-gas (GHG) emissions than short glass-reinforced resins while delivering the same mechanical properties.
In another sustainability-driven development, Polyplastics’ Duranex PBT has been selected for battery packs produced by Selex Motors, an electric motorcycle company from Vietnam.
About the Author(s)
You May Also Like