Whatever Happened to Metallocene-catalyzed PP?
Coming to market around the same time as its polyethylene partner, metallocene-catalyzed polypropylene is playing a more subdued, yet important, role in niche applications.
April 15, 2024
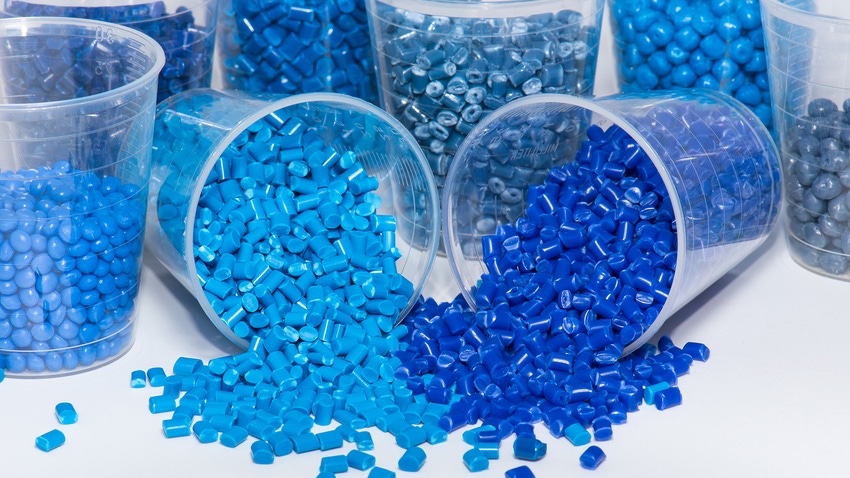
At a Glance
- Spunbond and meltblown hygiene and filtration usage dominates.
- Rigid injection-molded packaging benefits from optical properties.
- Potential automotive and medical applications have yet to be fully exploited.
Metallocene-catalyzed polypropylene (mPP) was developed around the same time as metallocene-based polyethylene (mPE), but sales of the two materials have been lopsided, with the mPE market perhaps 15 times larger. Nevertheless, mPP suppliers still hold hope that the resin will play a more prominent role in markets where purity and performance are priorities.
Maximizing hygiene potential.
MPP initially found its niche in the spunbond and meltblown nonwoven textile market, especially in the production of hygiene products such as diapers and wipes. It allows finer denier fibers to be produced, meaning not only reduced material usage but also the production of more drapable and softer textiles. In combination with propylene-based elastomers such as Vistamaxx from ExxonMobil Chemical, even softer, higher-loft, drapable nonwoven textiles can be realized.
LyondellBasell reports that its Metocene metallocene solutions are sparking a renewed interest in the textile industry, not only because of their downgaging capability but also on account of their low odor characteristics, a feature that is considered paramount in more-comfortable and discreet hygiene products.
A clear optical advantage in food packaging.
One standout application for mPP is injection-molded-film food packaging. This segment is another particular focus at supplier LyondellBasell. In an era where consumer safety and sustainability are paramount, the company’s Metocene grades are said to offer low odor, ensuring that taste and aroma of packaged food remain unaffected. This is a significant development for brands looking to maintain the organoleptic qualities of their products while reducing their environmental impact.
LyondellBasell metallocene solutions also address concerns about the use of highly regulated substances. With no phthalates or bismethoxyfluorene being used during the production of the product, LyondellBasell provides food packaging manufacturers with an alternative.
In addition to its numerous advantages in terms of safety and sustainability, Metocene-based grades also reportedly excel in enhancing the aesthetics of packaging solutions in terms of exceptional clarity and transparency, providing excellent visibility of the contents inside. This feature, often referred to as "shelf visibility," not only allows consumers to see the product they're purchasing but also adds a touch of elegance to the packaging.
Furthermore, metallocene solutions can impart a glossy and brilliant finish to the packaging, making it even more appealing on store shelves. This aesthetic appeal serves as a compelling selling point for brands across various industries, aligning with the growing demand for visually pleasing and attractive packaging solutions.
Automotive, medical applications show potential.
Albeit a niche market, several mPP suppliers including Korea’s LG Chem and TotalEnergies have earmarked mPP as having further potential in automotive interior applications on account of its low odor, minimal emissions of volatile organic compounds (VOCs), and fogging characteristics. These attributes are welcome given the increasingly stringent regulation of VOCs in Europe and elsewhere. Previously, Japan Polypropylene also demonstrated the ability of its Welnex metallocene TPO to eliminate weld lines and realize excellent surface appearance in glass-fiber-reinforced automotive interior components.
Further, mPP previously showed promise in sealant film applications but has since been outshined by materials such as Vistamaxx. There is, however, renewed interest in adoption in medical bags, where replacement of random PP copolymer and TPO materials is envisaged. Injection-molded medical device components are another potential outlet for mPP, as well as housewares and semiconductor transport trays.
About the Author(s)
You May Also Like