Feelin’ groovy? The Street Shark bionic surface reduces drag, enhances car performance
Mannheim, Germany — Shark skin, which has a special, grooved microstructure that reduces flow resistance, thus allowing sharks to move swiftly and efficiently through the water, has long been admired by engineers. Now, in a collaborative project with four other companies, Frimo, the Germany-based provider of system solutions for the manufacture of plastic components, has produced an artificial shark skin surface texture that works the same way - but on land for cars.
April 3, 2014
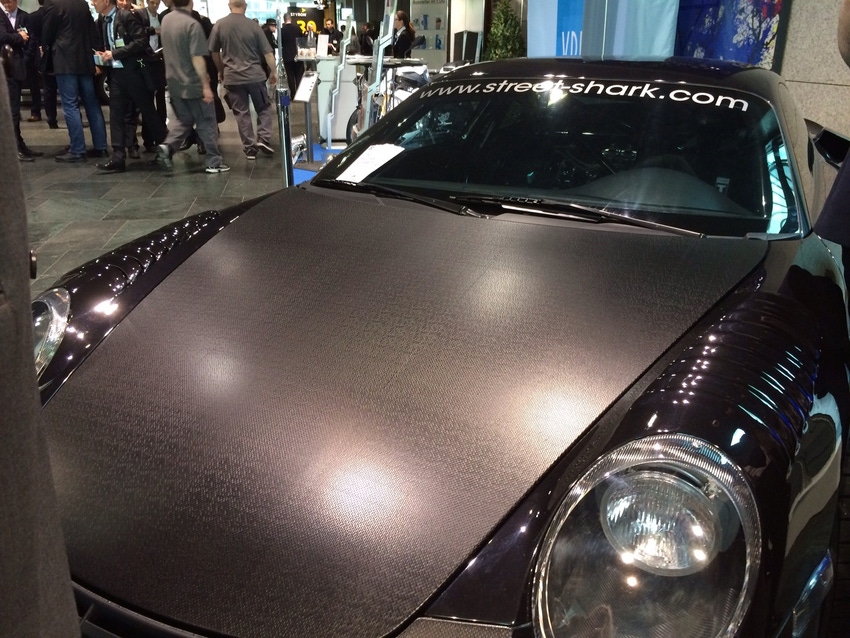
Mannheim, Germany — Shark skin, which has a special, grooved microstructure that reduces flow resistance, thus allowing sharks to move swiftly and efficiently through the water, has long been admired by engineers. Now, in a collaborative project with four other companies, Frimo, the Germany-based provider of system solutions for the manufacture of plastic components, has produced an artificial shark skin surface texture that works the same way - but on land for cars.
At this year's international Plastics in Automotive Engineering 2014 conference hosted by the German Association of Engineers (VDI) in Mannheim, a testosterone-boosting mean-looking number with a matte black Street Shark hood was one of the attractions on display.
For a number of years now, Frimo has been collaborating with Huntsman on the development of a new composite that used polyurethane, instead of epoxy, as a matrix material. Huntsman's polyurethane system technology is marketed under the name Vitrox.
Manfred Rudholzer, VP of sales at Frimo, explained it as follows: "Epoxy resins have a high viscosity, a long pressing time and a long curing time. We were looking for an alternative that would offer similar physical characteristics but would be more efficient to produce. Huntsman's Vitrox system was modified such that that low viscosity could be maintained for as long as desired after mixing, but after that it would immediately react and cure."
The reaction behavior significantly reduces the flow resistance required to fill the cavity, so only relatively low closing pressures are needed to keep molds closed. As Rudholzer pointed out: "As a 3D core sandwich material, we used PET, which we then injected with polyurethane at a low pressure of 50 mPa. In that way we obtained a strong, light composite material with the stiffness of PU."
The resulting prototype part weighed just 3.5 kilos, compared to 5.5 kilos using conventional resins, and fulfilled all the same requirements. Moreover, because a simple mold press was used, the new process is both cost-efficient and suitable for series production, as well as yielding possibilities for innovative bionic surface textures.
Rudholzer: "We wanted to use nature's characteristics for aerodynamics. Together with our development partner Eschmann-Textures, we created a tool with a shark surface texture. We built a positive model from a negative impression taken from a real shark skin, from which we then built a negative tool. We used an In Mold Coating (IMC) process, which enabled production of the finished component straight from the mold."
The first test modules produced in this way were the hood and roof module of a BMW Z4.
Wind tunnel testing showed that the use of the shark skin engine hood reduced the back pressure in front of the windscreen, which in turn also resulted in an improved drag coefficient value.
"The black matte prototype on display here today is new," Rudholzer said. "And we've had a lot of inquiries from interested carmakers."
Further testing is required, however. "Preferably by an OEM or Tier One supplier. For us, it passes all the tests, but what we need to do is to build two tools - one for expoxy resin, the other for the new process - for side-by-side testing by the industry."
He added: "The better aerodynamics means lower carbon emissions. And the shorter cycle times means more efficiency. That's two advantages already."
About the Author(s)
You May Also Like