The Troubleshooter: Preventing Speed- and Time-Related Defects in Injection Molded Parts
Incorrectly setting speeds and times associated with injection molding processes is one of the biggest causes of production failure.
February 2, 2024
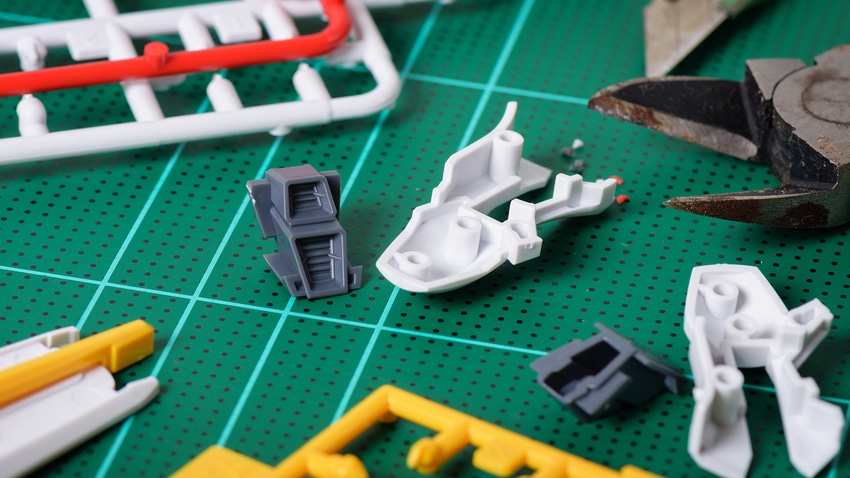
At a Glance
- Both too fast and too slow injection speeds can lead to defective products
- Compare screw rotation time with the cooling timer — the screw should recover 1.5 to 2 seconds before the timer runs out
- The cooling stage of a process also leads to process defects
In the world of plastic injection molding, scrap can cripple a company’s ability to turn a profit. Part defects can be caused by a multitude of molding factors, but speed and time settings associated with molding processes are among the biggest contributors to production failure. This article outlines various settings that can lead to molding defects. Understanding these effects can help processors make the appropriate adjustments to bring a process back to being a value-added commodity.
Injection speed
There are multiple scenarios where speeds within an injection profile can lead to defective products. Processes with a single injection speed during the fill stage are quite common, but in some instances they are less prudent owing to the complexity of the flow front as it moves through the runner system and cavity.
Injection speeds that are too fast at the beginning of fill can lead to splay or jetting. Speeds that are too slow in areas of ribs or tabs can cause overpacking and sticking. Too-fast speeds over or around part ribs or details can lead to shorts or poor knitting; at the end of fill, they can lead to burns and trapped gas defects. If the speeds at the end of fill are too slow, however, they can lead to shorts from trapped gas.
If multiple injection speeds may be of value, best practice is using the injection profiling procedure. Utilize injection positions and the position of transfer to evaluate how the flow front moves through the mold prior to transfer from injection to pack/hold. Speeds can then be adjusted based on actual screw positions as they relate to the defect area.
Screw recovery
Both speed and time can adversely affect the integrity of a process. Recovery times are longer at slower screw speeds, and shorter when screw RPMs are higher. The primary consideration is comparing screw rotation time with the cooling timer. The screw should recover 1.5 to 2 seconds before the cooling timer runs out and the mold opens.
Screw speeds running too fast can lead to poor mixing and blending. Premature recovery also allows material to settle to the bed of the barrel, which can lead to material being baked by heater bands, causing splay. Recovery times longer than the cooling timer lead to inconsistent cycle times and poor process consistency.
It is also important to note that back pressure directly affects rotate time. Increasing back pressure increases the rotate time. Lowering back pressure leads to a shorter rotate time.
Decompression after rotate
Speed is the primary concern in terms of screw decompression. Viscosity is a primary factor in terms of how quickly or slowly the screw should decompress once shot size has been achieved. Sucking back too quickly can cause splay. Slow decompression can lead to the check ring not seating properly and an inconsistent cushion.
Mold and ejector speeds
The most obvious effect that slow mold opening and closing speeds have is on cycle time.
Faster cycle times generally lead to better process consistency. It is, however, important to note that it is possible to run too fast. Operators need adequate time to properly inspect parts and perform their duties.
It is also important to note that mold complexity directly affects mold opening and closing speeds. Simple molds can open and close faster than those with slides, multiple pins, or complex detailing. Keeping molds safe from damage should always take priority over mold open and close speeds.
Understanding ejector speed setup is also important. The primary goal is to quickly eject parts using minimum stroke. Maximizing the ejector stroke adds time to the cycle and leads to faster wear of ejector components. Keep in mind that ejecting too quickly can cause inconsistencies in part removal and pin push defects.
Cooling
The cooling stage of a process also leads to process defects. Parts that must meet dimensional requirements can be adversely affected by — or benefit from — cooling stage effects.
Parts ejected prematurely can shrink more than those that remain in the tool longer. In addition, part form is largely determined by the amount of time it remains in the core cavity of the mold. Part lengths can be shorter if cooling time is too short. In addition, opening the mold prematurely can lead to the part not having enough time to shrink to the core half of the mold: As the mold opens, the part sticks in the stationary half of the mold. Part warp can also br directly related to the length of the cooling timer.
In conclusion, process timers and speeds can clearly define the consistency of production efficiency. While slower speeds can undoubtedly affect cycle times and part consistency, faster speeds and times can also have an adverse effect. By understanding the causes and effects of these molding conditions, we are better able to set our speeds and timers based on best molding practices and results.
Got a problem with this, that, or the other thing? You might find answers in some previous "Troubleshooter" columns:
How to Identify and Correct Shear-Related Splay Defects
The Role of Moisture in Injection Molding Splay Defects
Preventing Flash in Injection Molded Parts
How to Prevent Common Failure Modes in Injection Molding
Building a Validated Plastic Injection Molding Process
Fixing Color Defects in Injection Molded Parts
Key Steps for a Stable Injection Molding Process
Fundamentals of an Injection Molding Plant or Cell Startup
What to Consider When Buying an Injection Molding Machine
About the Author(s)
You May Also Like